University of Maryland: Microfluidic System for Robotic that can Play Nintendo
Integrated fluidic circuitry, 3d printer microfluidics, 3d printing microfluidics.
The BAM Laboratory, directed by Prof. Ryan D. Sochol, is a group of researchers at the A. James Clarck school of engineering, University of Maryland, College Park, USA. The BAM Lab focuses on pioneering alternative micro/nanofabrication strategies based on state-of-the-art additive manufacturing technologies, or “3D printing”, to advance biomedical fields. More specifically, they focus on cases requiring device architectures and/or functionalities that would be difficult or infeasible to achieve using conventional manufacturing methods.
Recent research topics include 3D Microfluidic Technologies via Direct Laser Writing, Multi-Material Direct Laser Writing, and 3D-printed soft robotics with fluidic circuitry. In the latter topic, the group recently designed and actuated a soft robotic turtle and a microfluidic system for robotic hand by means of pressure. This work was published in Science Advances.
Microfluidic system for robotic
Playing Mario with a 3D Printed Soft Robotic Hand with “Integrated Fluidic Circuitry”
Introduction
Over the past decade, the field of soft robotics has established itself as distinctively suited for applications that would be difficult or impossible to realize using traditional, rigid robots1,2. “Soft robotics” and microfluidic system for robotic center on creating new types of flexible, inflatable robots that are powered using water or air, and integrated fluidic circuitry rather than electricity. Using compliant materials actuated by fluidic means brings several benefits, particularly in terms of safety for human-robot interactions, lower costs, and adaptability in geometry for manipulating complex and/or delicate objects1 (for instance, soft robotic sleeves for pumping ailing hearts). However, the emergence of microfluidic systems for robotics has presented new challenges associated with controlling the underlying fluidics of such systems. Fabrication of fully-embedded soft robots (i.e. including soft actuators; body features; and integrated fluidic circuitry) can be challenging depending on the manufacturing method. In addition to manufacturing challenges, stable and fast fluidic control is often a prerequisite for the great functioning of soft robots.
Ryan Sochol’s group addressed manufacturing challenges by developing a novel strategy for additively manufacturing unified soft robotic microfluidic systems with fully integrated fluidic circuitry in a single print run via multimaterial “PolyJet three-dimensional (3D) printing microfluidics”. It is an inkjet-based process by which multiple photoreactive materials are dispensed in parallel to produce multi-material 3D objects in a line-by-line, layer-by-layer manner1. To ensure stable flow and fast-response actuation, the group used Fluigent pressure-based flow controllers and dedicated software.
In a microfluidic research paper published in 2021, the group designed several soft robots and investigated their operation performances. Here, we summarize partial results obtained with the soft robotic hand.
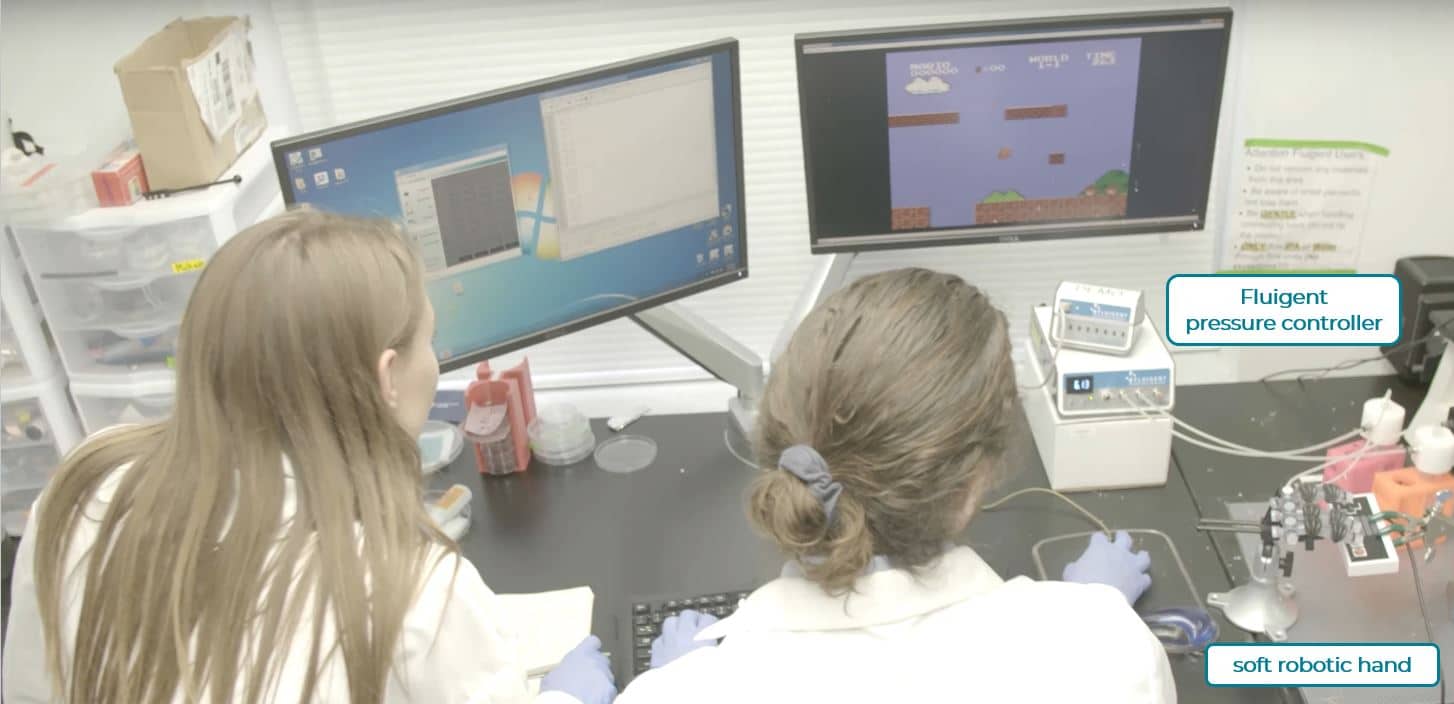
Fluigent microfluidic system for robotic
Soft robotic turtles and a soft robotic hand were first produced by PolyJet 3D printing, and finite element analysis simulations were performed to predict the input pressures required for robot actuation. In addition, circuits elements characterization was performed using Fluigent Flow Units. More information about the design of the soft robots as well as their characterization can be found in the paper1.
To experiment the operation of the soft robotic hand with integrated fluidic circuitry, the group programmed the hand in order to play the Nintendo Entertainment System (NES) Super Mario Bros. video game in real time using a controller. Figure 1 illustrates the setup used for fluidic actuation. All experiments were performed using Fluigent pressure controllers along with the corresponding software. Pressure controllers are connected to two reservoirs, which are connected to inputs of the fluidic hand. Note that in the paper Fluigent MFCS were used, but we now provide the Flow EZ, more compact, and permitting local control if needed.
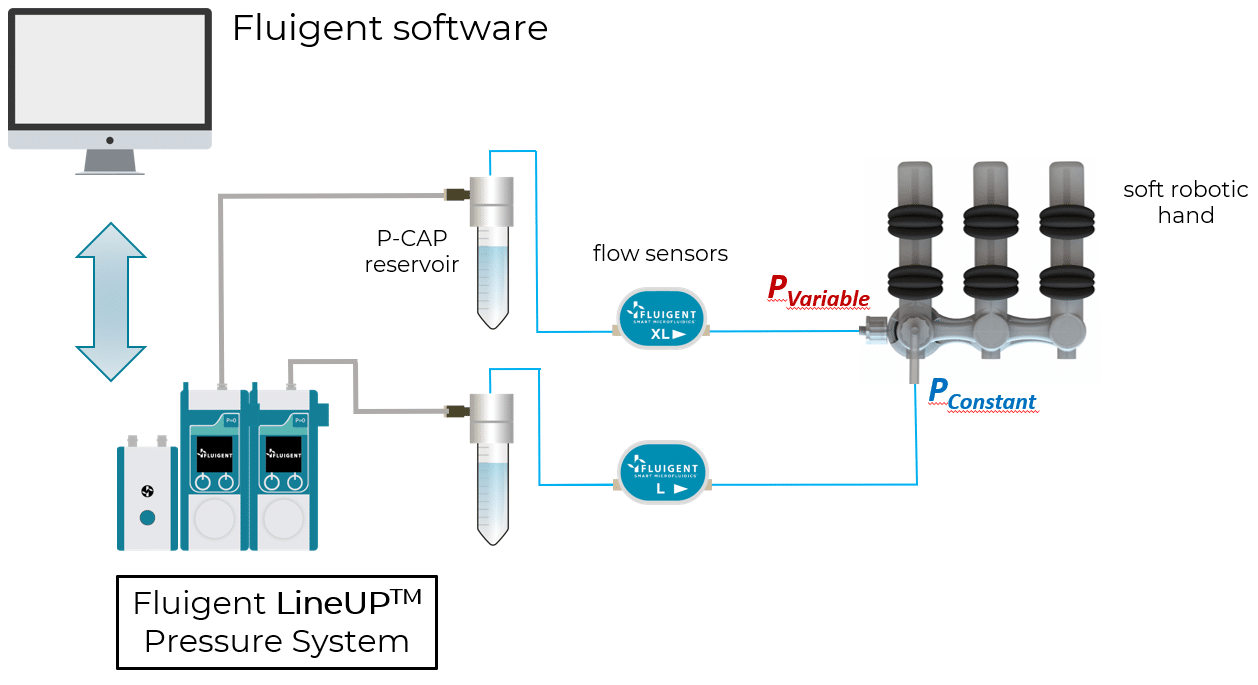
An input is kept at constant pressure (PSource = Ps) while the second input is dynamically regulated for actuating the hand (PGate = Pg) (figure below). Pneumatic experiments are performed by running a custom script via the Fluigent MAESFLO software (now OxyGEN) and Fluigent script module to dynamically regulate the Pg input while maintaining a constant Ps. The soft robotic hand is fixed in place using a clamp, while the base of each fingertip is affixed to the corresponding NES controller button.
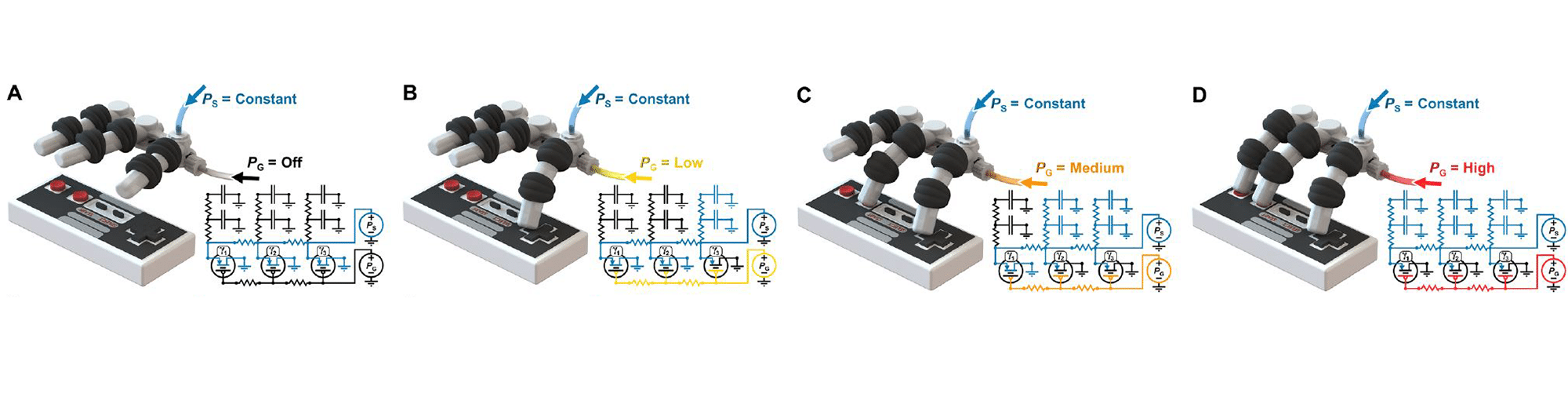
Partial results
In this work, a constant Ps input of 18.5 kPa is used, allowing for four Pg states: (i) Pg,Off ≤ 5 kPa, none of the buttons are pressed—Mario is immobile (Fig. 3 i); (ii) Pg,Low ≥ 20 kPa, the right button of the D-pad is pressed—Mario walks (Fig. 3 i); (iii) Pg,Medium ≥ 40 kPa, the B button is also pressed—Mario runs (Fig. 3 iii); and (iv) Pg,High ≥ 60 kPa, all of the buttons are pressed—Mario jumps (Fig. 3 iv)1. It is possible to observe fast response time and high pressure stability for all states.
By taking into considerations time required when executing inflations or deflations in designing the program, the authors managed to complete the first level of Super Mario Bros. in real time, as shown in the short movie below!
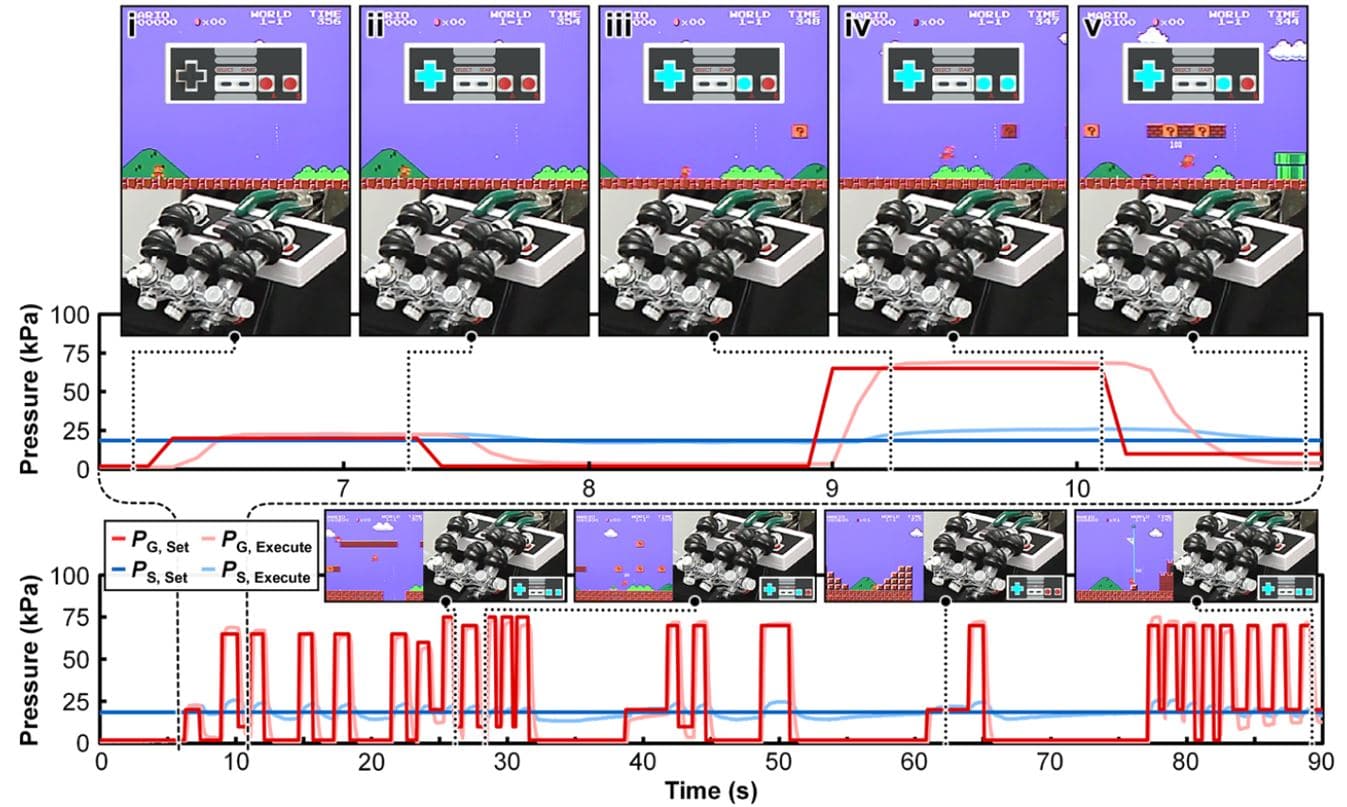
Conclusion
The study successfully demonstrated the use of a microfluidic system for robotic applications. The system, which used Fluigent pressure-based flow controllers, Fluigent Flow Units, and dedicated software, provided precise and fast actuation, surpassing conventional methods. This microfluidic system for robotic control not only enhanced the efficiency and responsiveness of the soft robotic hand but also opens new possibilities in the field of soft robotics by allowing for more complex movements and tasks.
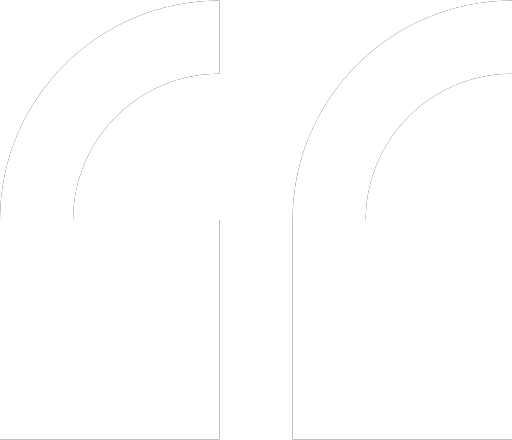
“Typically, each appendage of a soft robot would typically need its own control line, which can limit portability and usefulness, but by 3D printing soft robots with integrated microfluidic circuits and networks, they can be controlled based on just one pressure input. Enhancing soft robot autonomy in this manner is critical for our emerging applications like soft robotic surgical tools. Controlling soft robots based on a single pressure input is founded on the ability to precisely regulate the pressure magnitude at set times – a capability that we found the MFCS and accompanying Maesflo software (now OxyGEN) was uniquely suited for accomplishing.”
Prof. Ryan D. Sochol
References
- Hubbard, J. D. et al. Fully 3D-printed soft robots with integrated fluidic circuitry. Sci. Adv. 7, (2021).
- Sochol, R. D. et al. 3D printed microfluidic circuitry via multijet-based additive manufacturing. Lab Chip 16, 668–678 (2016).
More information
Expertises & Resources
-
Expert Reviews: Basics of Microfluidics Choosing the Right Microfluidic Pressure Range Read more
-
Microfluidics White Papers An exploration of Microfluidic technology and fluid handling Read more
-
Expert Reviews: Basics of Microfluidics Flow Control Technologies: Comparison between peristaltic, syringe and pressure pumps for microfluidic applications Read more