5 reasons to choose OEM pressure controllers over OEM syringe pumps for microfluidic applications
When integrating OEM flow control components into Diagnostic or Life Sciences systems based on microfluidic technologies, OEM syringe pumps are widely used. Yet, they show strong limitations both in terms of performance and reliability. An alternative to syringe pumps is pressure controllers. Here, we highlight the main reasons why one should consider moving from Industrial syringe pumps to OEM pressure controllers for microfluidic liquid handling.
1. Pressure control for unmatched performance
A stable and precise flow rate, with a fast settling time, is often a prerequisite in microfluidic and millifluidic applications such as droplet microfluidics, drug screening, cell analysis, or dynamic cell culture for cell biology and microscopy.

Pressure control for improved stability and settling time
A stable and precise flow rate, with a fast settling time, is often a prerequisite in microfluidic and millifluidic applications such as droplet microfluidics, drug screening, cell analysis, or dynamic cell culture for cell biology and microscopy.
In a system that generates microfluidic droplets, a fast settling time (defined as the amount of time for the output signal to reach a certain percentage – for instance, 95% – of an instantaneous pressure change) is generally needed to directly reach the targeted flow rate, and subsequently, the required droplet size related to it. This allows for the minimizing of the transient phase, where generated droplets (that can contain expensive reagents or cells) cannot be exploited. This ultimately reduces waste and costs of the microfluidic protocol. On the other hand, a stable flow rate ensures homogeneous droplet size, ensuring the long-term reliability of your protocol. .
a. Settling time: what is the real flow rate in your system?
OEM Syringe pump and settling time
Industrial syringe pumps consist of a simple source of linear motion induced by a stepper motor that controls the speed at which the piston is driven. The flow rate is directly deduced by the piston velocity and section. The settling time not only depends on the mechanics of the syringe pump but also on the fluidic resistance of the microfluidic system. When implementing or modifying the ordered flow rate, the internal pressure increases in the fluidic system and deforms it instead of pushing the liquid.
Depending on the system’s fluidic resistance and elasticity, the settling time varies from a hundredth of a millisecond to several minutes. When implementing a flow rate on the syringe pump for industrial applications, the ordered flow rate value is displayed, but there is no information on the actual flow rate, or the time required to reach it. The microfluidic device’s lack of information on the real flow rate is one of the main sources of experimental and protocol failure.
Fastest response time with OEM pressure controller
Pressure controllers allow for the pressurizing of the reservoir or tank that contains your liquids. When using a pressure controller, pressure is almost instantaneously applied to the reservoir. For instance, valves used in Fluigent instruments usually have response times below 30 milliseconds, which is lower than motors used in syringe pumps. Reactive systems such as the F-OEM and its FASTAB technology have fast settling times. The graph below shows the response times of a Fluigent F-OEM pressure controller with a standard syringe pump. Targeted pressure is
achieved in less than a few seconds for the majority of fluidic systems (depends mainly on the pressure source and related gas flow rate, and the pneumatic volumes to be pressurized). the pneumatic volumes to be pressurized).
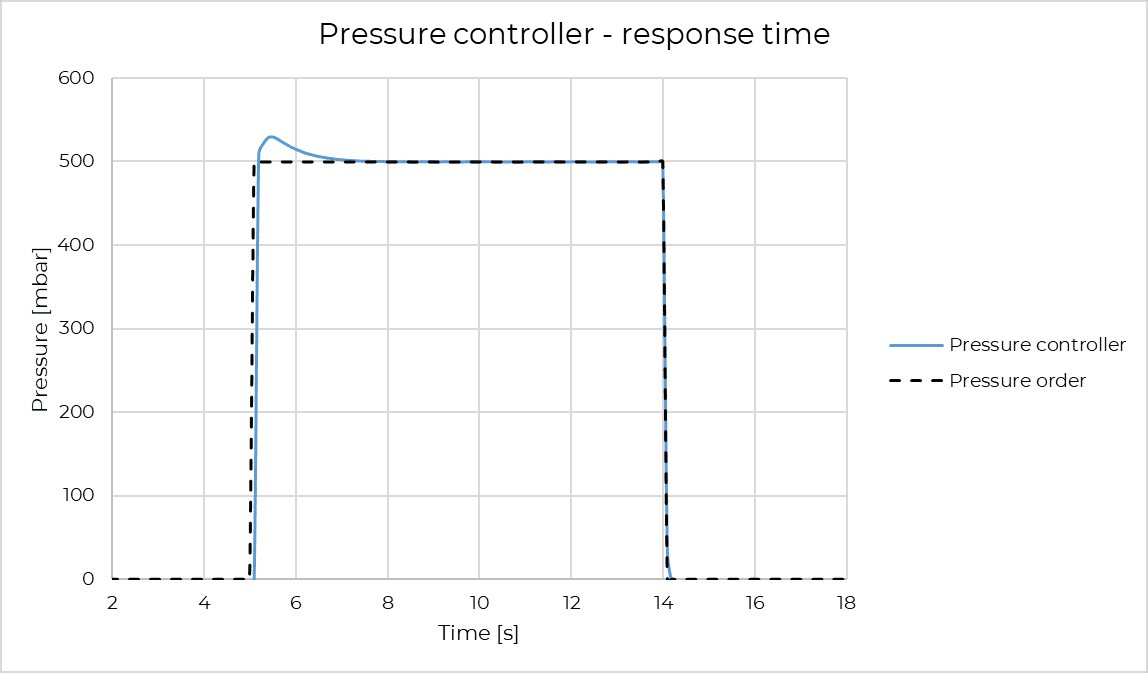
Figure 1: Response time between pressure –based flow controller
b. Unmatched stability thanks to finely adjusted pressure
The flow stability of a syringe pump is inherent to the minimal mechanical step supplied by its motor. Because the piston’s increment is correlated to the volume injected, this minimal movement induces a minimal injected volume. The stepper motor will induce pulses or oscillations at low flow rates that are related to the technology and not due to external parameters. Consequently, most syringe pumps on the market cannot reach a stability lower than 0.35%, which is already for high-end syringe pumps that make use of low-volume syringes as a smaller diameter and – ~10 ml syringes – improve stability (but inevitably affect volumes to be injected and maximum flow rates that can be reached).
When a reservoir or a tank is pressurized using a pressure controller, the sample is smoothly injected into your microfluidic system. This technology generally makes use of solenoid valves, allowing for extremely fine-tuning of the pressure applied. As there are no mechanical parts in contact with the fluids, pressure controllers can establish pulseless flows that cannot be obtained with even the most accurate syringe pump. Using Fluigent controllers, pressure stability with < 0.1% CV is obtained. This allows a new level of stability that is required for emerging applications.
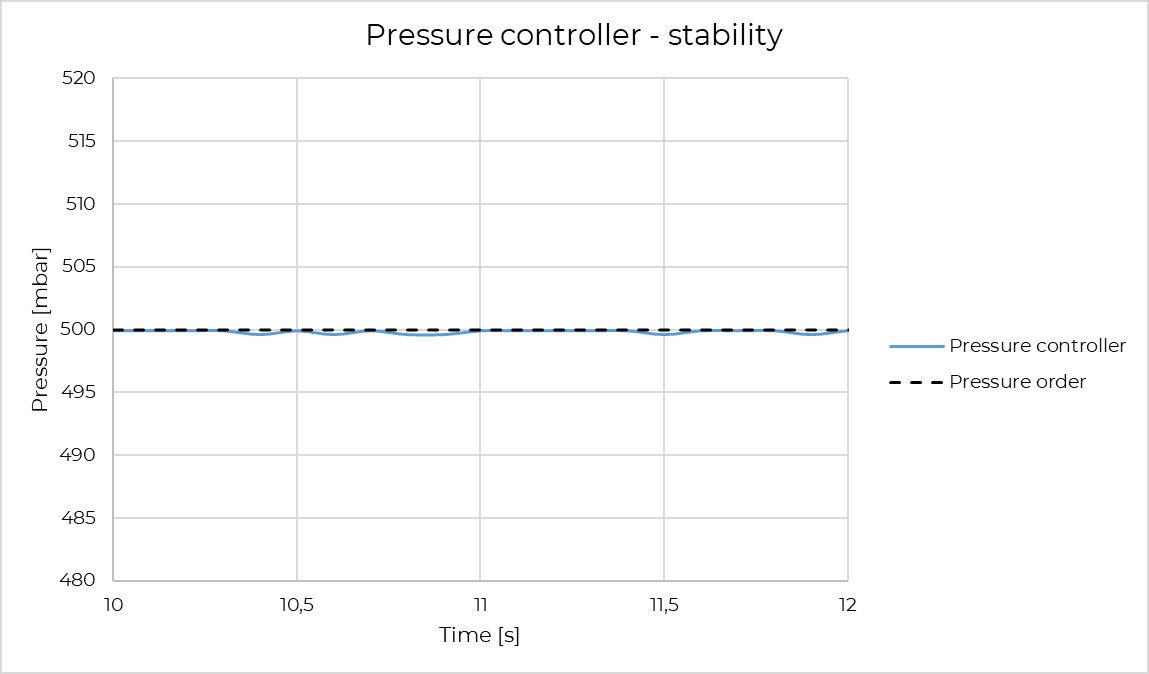
Figure 2: Pressure stability pressure –based flow controller
c. Higher liquid flow rate accuracy and regulation capabilities with a flow sensor: pressure-driven flow control
Inline flow sensors for fast, accurate flow rate monitoring & regulation
If one wants to directly measure the flow rate, a liquid flow sensor can be added to the system. Flow sensors are also useful to ensure a fluidic protocol’s proper functioning, permitting flow/volume monitoring, or protocol failure identification and prevention. Flow sensors are complementary to pressure controllers as they permit to develop a “feedback loop” system, regulating the flow rate through pressure if an algorithm is implemented. Fluigent offers pressure-based flow rate regulation due to its patented “self-learning” algorithm, allowing the flow rate to be adjusted while an experiment is running to control the sample volume dispensed and/or the sample flow rate. The graph below compares flow rate stability between Fluigent pressure-based flow control and a standard OEM syringe pump. Using our regulation algorithm coupled with a flow sensor, a flow rate stability of < 5% is achieved, while ~10% stability is observed with a syringe pump.
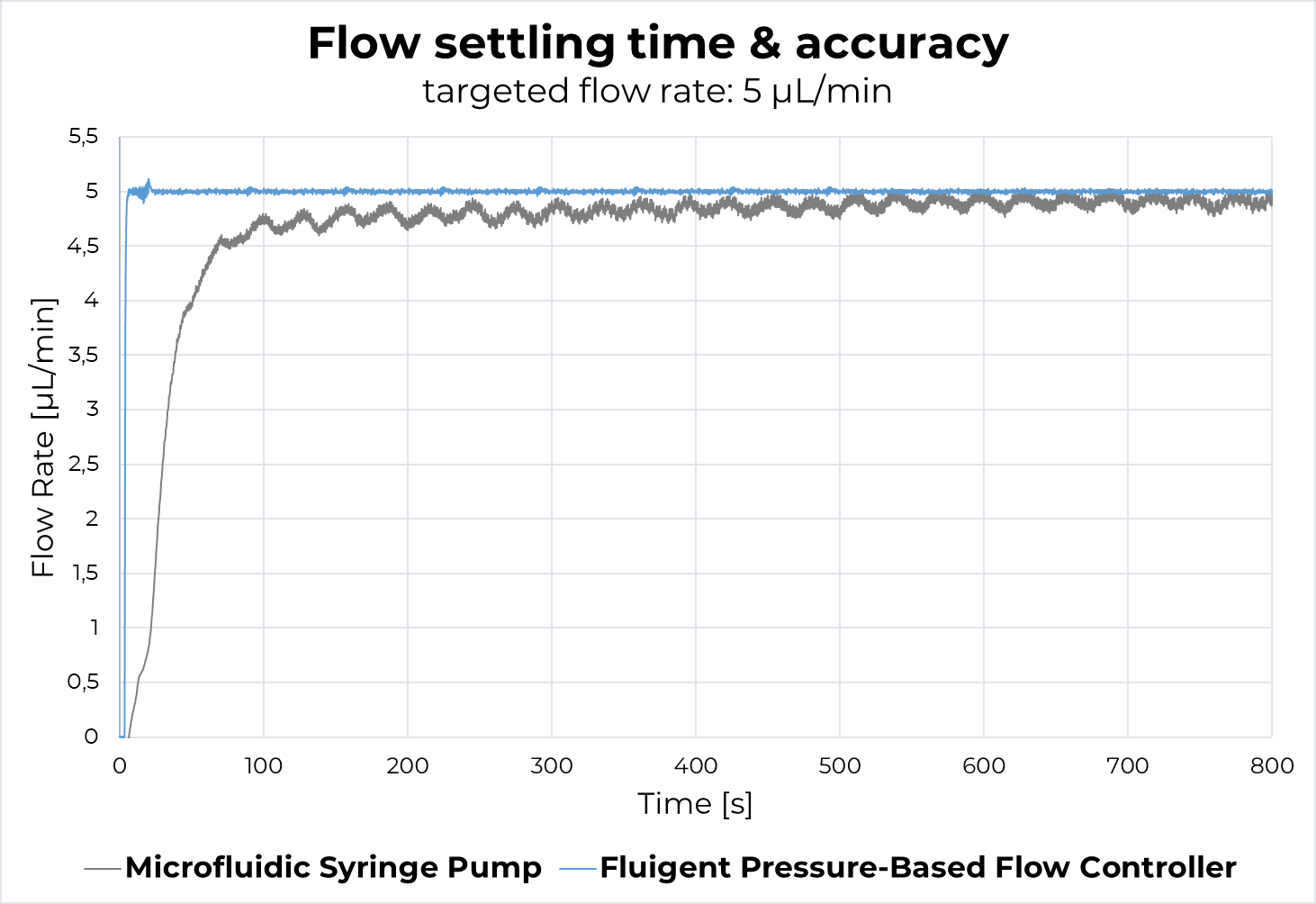
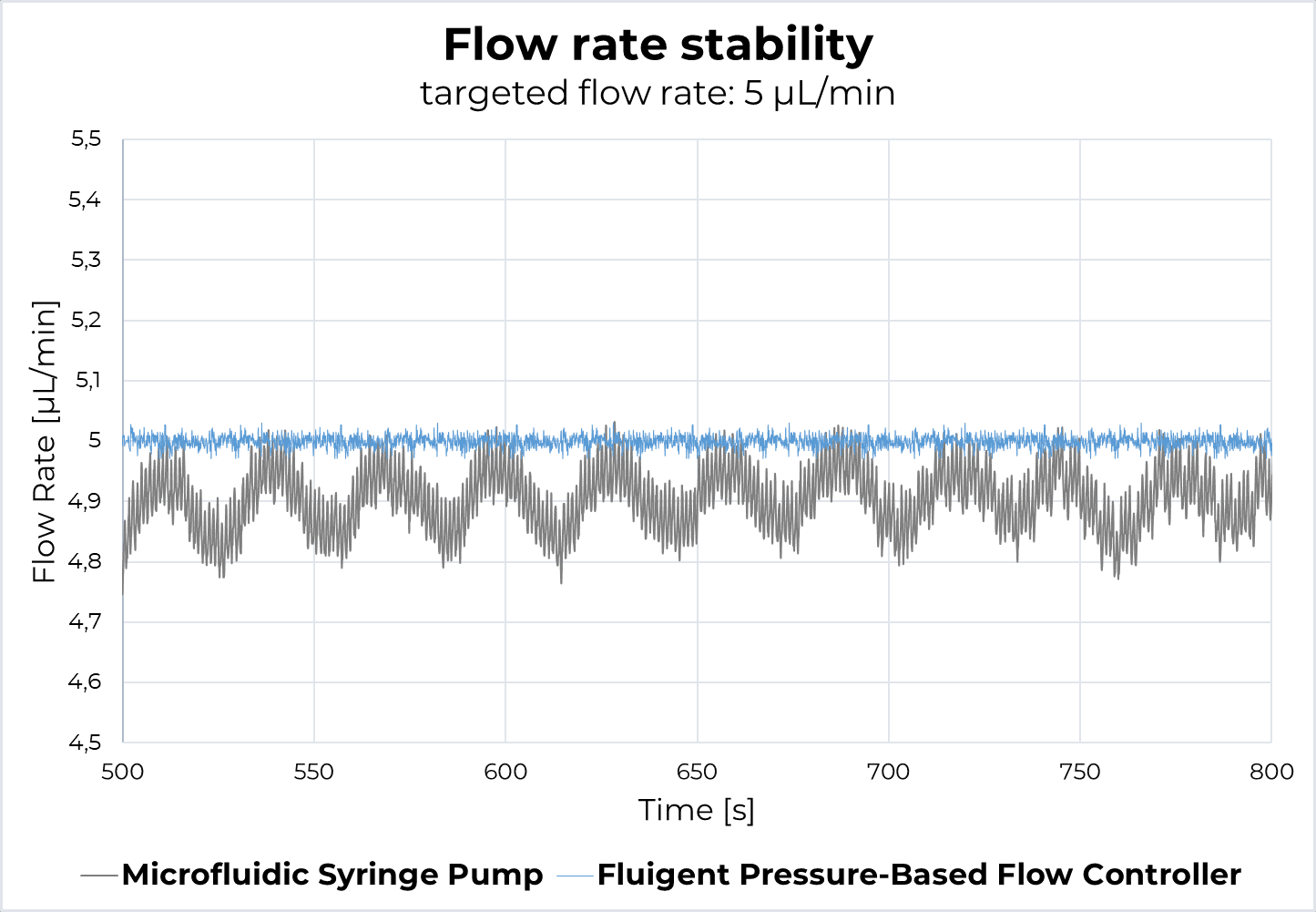
Figure 3: comparison between an OEM syringe pump (grey) & an OEM pressure-based flow controller (blue)
Need high-performance pressure-driven flow control without having a flow sensor on the fluidic line?
With the growth of biological applications that make use of microfluidics, the need for a fully sterile, and disposable environment on the fluidic line is intensely growing. Fluigent is the only company to provide a non-invasive flow sensor dedicated to fluidic applications.
Fluigent’s standard OEM pressure-based flow control solution, which consists of a high-precision pressure controller (Fluigent PX or F-OEM) and a Non-Invasive Flow Sensor, brings excellent flow rate regulation without requiring elements on the fluidic path or fluid calibration. The NIFS allows contactless live flow rate monitoring and regulation.
This unique system keeps Fluigent a step ahead of other microfluidic pressure-driven flow control providers as well as industrial syringe pump suppliers.
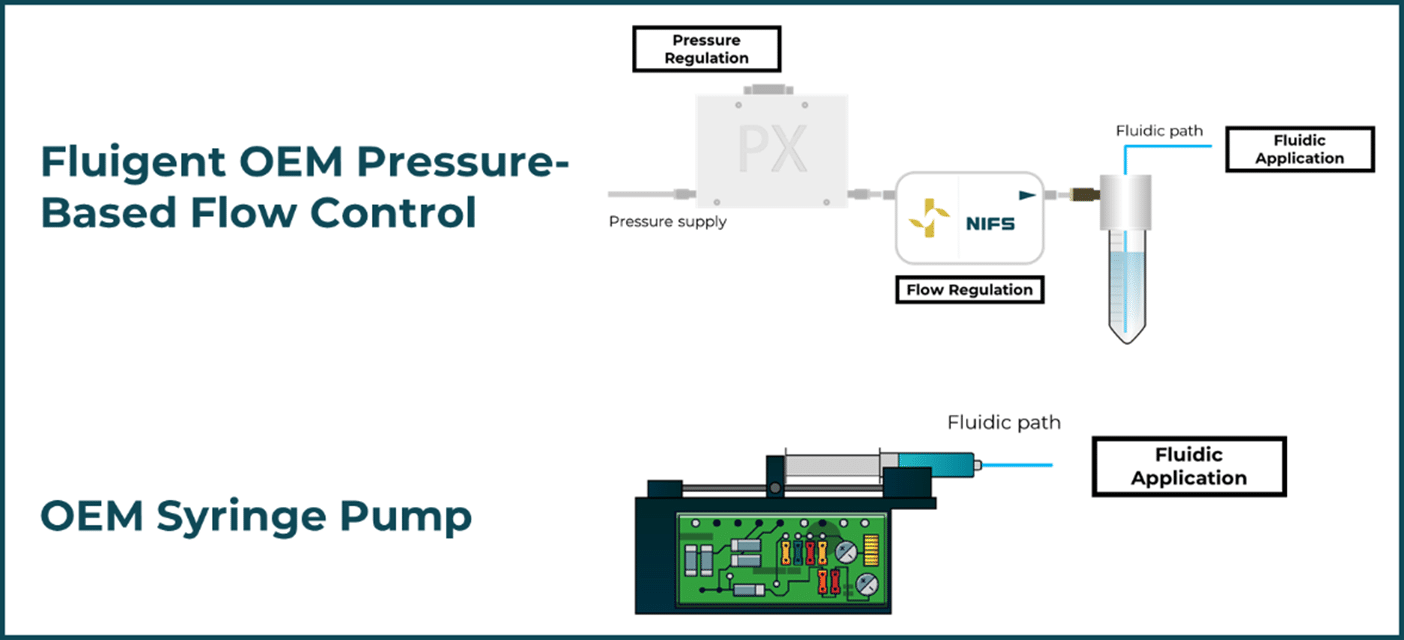
Figure 4: syringe pump system vs Fluigent pressure-based flow control system
Fluigent Pressure Controllers | OEM Syringe Pump | |
---|---|---|
Accuracy | < 0.1% CV Full Scale (FS) | ~ 1% |
Pressure Resolution (Minimum pressure steps) | 0.03% FS | N/A |
Response time | Pressure controller: < 30 ms | N/A |
Settling time | Pressure: < 2 s Flow rate: < 5 s | From a few seconds to minutes depending on the fluidic system |
Outlet pressure range | Positive range: 0 to 25 mbar, 0 to 69 mbar, 0 to 345 mbar, 0 to 1000 mbar, 0 to 2000 mbar, 0 to 7000 mbar Negative range: 0 to -25 mbar, 0 to -69 mbar, 0 to -345 mbar, 0 to -800 mbar Push-Pull: -800 to +1000 mbar | N/A |
Liquid Flow Rate Range | 0 to 10 mL/min | > 200 mL/min |
Injection volumes | Up to 1 L | < 140 mL (Limited by max. syringe size) |
Flow rate monitoring & regulation | Using a flow sensor: < 5% m.v. | No live monitoring. |
Compatibility with sterile environments / Contamination risks | Suitable Sterile reservoirs and no mechanical parts in touch with the liquids Flow rate control possible without any system on the fluidic line with the NIFS | Possible Disposable plastic syringes OK, but decreased performance Glass syringes: Needs sterilization/cleaning step for each experiment |
Compatibility with long-term protocols | Suitable Stable pressure supply | Limited by syringe reservoir Prone to instability over time depending on the syringe pump and syringe used |
Maintenance | Not required | Syringe alignment, seal maintenance |
2. No need to compromise stability for larger injection volumes anymore. Gain time on implementation and refills.
As explained above, the larger the syringe volume (more specifically, the section), the lower the flow rate stability. Consequently, syringe pump users need to choose between stability and minimum volume in order to be injected, which is not always possible depending on the targeted application. In addition, most syringe pumps dedicated to microfluidic industrial application do not exceed 60 mL volume, which can be a strong limitation for any applications that need buffer solutions.
When using pressure controllers, it is possible to use larger reservoirs. With Fluigent pressure systems, bottles of up to 1 L can be used without affecting the excellent flow stability provided by pressure. Filling and refilling processes are straightforward using pressure-based systems.
3. A Cost-effective solution for your microfluidic system
At first sight, a pressure-driven flow control system can look more costly than a syringe pump system, as the addition of a pressure source and flow sensors (if required) add up to the cost of the overall system. However, some advantages of pressure controllers and continuous technology improvement ultimately affect the final cost of your system, including:
- One channel to feed several reservoirs
It is possible to pressurize several reservoirs using one pressure controller, which is less feasible with syringe pumps as flow rates are not likely evenly separated.
- Better response time means less reagent consumption and waste
As explained above, during the transient phase where flow rates are not stable, data cannot be exploited, and reagents used during this phase are lost. Minimizing this transient phase allows for optimizing reagent consumption thus reducing experimental costs.
- All-in-one pressure source and control to reduce the overall cost
The latest technology developed by Fluigent: a Compact All-In-One Microfluidic Micropump offers integrated pressure supply and control (positive and negative pressure) in a light and compact format (L*l*H = 7*5*4 cm), a cost-effective technology with a unique level of compactness at a reduced cost.
4. Reducing hazards due to cleaning issues and contamination
Using a high-precision syringe pump requires non-disposable glass, steel, or ceramic syringes as plastic syringe deformability impacts stability. Those non-disposable syringes are generally not delivered sterilized. This is a limitation for many biological applications where sterility on the fluidic path is mandatory. In addition, when using reusable syringes, cleaning is required, which in addition to being a tedious step, is more importantly an additional risk of contamination that could lead to experimental failure.
When using pressure controllers, no mechanical parts are in contact with the liquid. One can use standard disposable tubes or reservoirs that can come sterilized if needed. Contamination risks are thus mitigated using a pressure controller compared to an OEM syringe pump.
5. Cut down maintenance with pressure controllers
When developing a microfluidic system integrating liquid handling components, it is important to consider the lifecycle of all parts as well as the required maintenance needed to extend the lifetime of your system. When using syringe pumps, time-consuming maintenance steps are required to avoid degraded performance or protocol failure:
- Alignment steps: An incorrect syringe alignment and installation would impact both precision and accuracy. It is also a source of damaging syringe seals due to excessive installation forces. This must be done after every syringe replacement.
- Sealing maintenance: if pump seals are not properly maintained over time, leakage can occur and would lead to less accurate dispensing. Plunger seals often also contain a thin film of silicon oil lubricant that wears away over time as a result of use and exposure to fluids. Re-lubricating maintenance is periodically necessary to avoid performance issues or damage.
Maintenance is drastically reduced when using pressure controllers as they are not in contact with fluids. Securing a clean pressure source is usually enough for your pressure controller to work properly for several years. No alignment or calibration steps are needed before starting a protocol, unlike syringe pumps for industrial applications. Pressure controllers ensure a prolonged system lifetime, reducing time spent with Fluigent support.
As an expert and leader in accurate liquid control and automation, Fluigent provides innovative OEM instruments and customization services for manufacturers from Life Sciences to Diagnostics.
Related Products
Fully Custom Microfluidic Device
See productMicrofluidic Flow Management Unit
See productModular OEM Microfluidic Flow Controller
See productMicrofluidic OEM Pressure Controller
See productMicrofluidic OEM Flow Sensor
See product