Ensuring Quality Control in Micro-Scale Devices by Innovative Leak Detection Method
Long term performance and reliability characterization are essential when developing or producing microfluidic or other devices. To ensure the reliability and the sealing integrity of devices, rigorous quality control testing is essential. Micro leakage detection is one parameter to control.
This application note discusses the importance of leak detection on a micro scale and various methodologies to perform it. The Leakage Testing Pack is used to conduct a liquid-based burst test on a device for detecting and characterizing micro and nanoleaks using pressure-based flow controllers.
Why Performing Quality Control for Microfluidics Devices?
Micro-scale devices have applications across multiple fields, including preventive medicine, pharmacology, and environmental sciences.
To ensure the safety and efficacy of microfluidic systems, rigorous quality testing is usually necessary. When developing a microfluidic system, particular attention should be paid to micro-leakages. In fact, they can compromise the performance of these systems. These can arise from various factors, including material quality, mechanical stress, manufacturing defects, or material aging. These issues can lead to a loss of reliability and device functionality, which can ultimately lead to product failures (e.g., loss of valuable samples, poor repeatability).
Leakage characterization can be performed during system qualification. In microfabrication, for example, it is essential to verify the integrity of microchannels at different pressures or flow rates. In digital PCR applications, leakage testing of valves is critical to ensure accurate results [1]. Furthermore, leak detection is critical in lab-on-chip and organ-on-chip systems, where maintaining a sealed environment is essential [2]. Several methods can be used to characterize leaks of a microfluidic device.
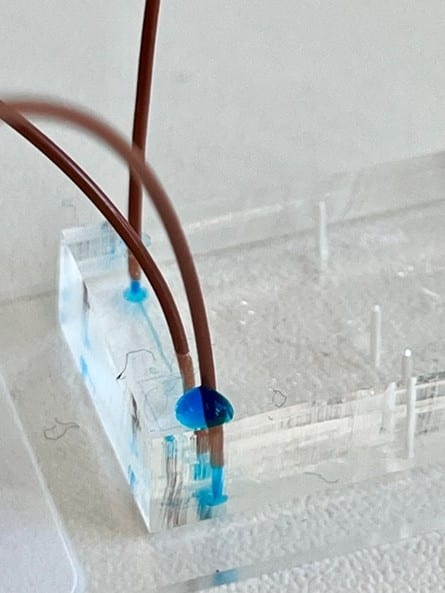
Different Methods for Micro-Leak Detection
In leak detection, gas-based and liquid-based methods are used to assess device reliability under different conditions.
The maximum operational pressure test evaluates if a device can withstand standard operational pressures without leaking, useful for quality control before distribution [3]. In contrast, the burst test is a destructive test used to determine the device’s maximum pressure tolerance before failure and to assess its structural limits.
Gas-based testing
The gas-based leak detection method involves measuring gas escaping from the system. It is conducted on a closed system by applying pressure, monitored by a pneumatic sensor or pressure transducer. A pressure drop indicates the presence of a leak. This method’s main advantages are its non-contaminating and non-destructive nature. With precise measurements, it is also a highly sensitive method.
Precautions like using dry air or inert gases such as nitrogen should be taken to prevent device damage, or minimizing the test setup’s internal volume helps optimize manometer sensitivity [3]. One challenge is correlating the gas leakage rate to the medium’s leakage rate, as viscosity differences may affect results [4]. For this reason, this method is more effective for qualitative rather than quantitative approach.
Liquid-based testing
Liquid-based testing methods utilize external pressure sources and manometers to pressurize a sealed system filled with liquid. Typically, leak detection is done by gradually increasing the pressure; once the source is disconnected, any pressure drop indicates a leak. These methods traditionally use industrial pressure controllers that are limited in precision, as they do not have a fine enough measurement scale. The process can also be time-consuming, requiring computer integration and manual adjustments for both pressure control and flow rate measurement. This complexity adversely affects the performance, speed and consistency of quality control.
To address these challenges, Fluigent’s technology offers a fully automated solution with advanced pressure-based flow controllers and high-sensitivity flow sensors that can detect leaks as small as nanoleaks. Moreover, our user-friendly software streamlines the testing process, enabling quick and accurate quantification of leakage rates. This leakage test pack reduces testing time and significantly improves reliability, performance and precision. It is valuable for characterizing components during development and for quality control at the end of the industrialization process.
Liquid-Based Burst Test and Leak Detection Method Using Precise Flow Control
A burst test using a PDMS microfluidic chip was performed, allowing to assess the pressure tolerance and burst threshold of the microfluidic channels. This type of analysis is crucial for ensuring component durability under high-pressure conditions.
Material & Methods
To perform the test, the Leakage Testing Pack is used. The Flow-EZ pressure controller is used to apply pressure on the system. A flow sensor and a pressure sensor are employed to accurately detect and measure variations in pressure and flow rate upstream of the chip. During the experiment, a flow rate remaining at zero and a stable pressure measurement demonstrates the integrity of the system. If a positive flow or pressure drop is observed, this indicates a leak, which can be quantified precisely through flow rate measurements.
- The microfluidic chip is sealed so that the system is closed.
- The device is filled with DI water (colored water is used here in order to identify the location of the leak).
- Low pressure is applied, for 30 min so the system can stabilize.
- Pressure steps from 0 to 3 bar are programmed and maintained for 3 min at each step. This step can be automated using OxyGEN software, which enables the protocol to be created, applied and saved.
Results and discussion: Nano-Leak Detection and Chip Delamination
The evolution of pressure and flow rate measurements was measured over time while the applied pressure was increasing gradually (Figure 4).
Above 2250 mbar, a flow rate of hundreds of nL/min is recorded, indicating the first leaks which correspond to partial damage of the microfluidic channels (picture 1).
As the applied pressure reaches 3000 mbar, complete delamination of the chip is observed (picture 2), resulting in significantly higher leakage rates of approximately 5 µL/min. This sudden increase in leakage is accompanied by a noticeable drop and instability in the pressure measurements by the sensor due to a decrease in the system resistance and a loss of system containment.
These results highlight the device’s precision in early leak detection. With the ability to detect flow rates as low as nL/min, this system can accurately quantify leakage rates, enabling users to assess the severity of leaks. This capability provides critical data for effective characterization and quality validation in microfluidic applications.
2. Leakage due to chip delamination.
Figure 4: Graph showing the evolution of pressure and flow rate measurements over time during the chip burst test, with images illustrating the corresponding leakage visualization.
Conclusion and Outlook
This application note highlights how flow and pressure control systems enable rigorous liquid-based leakage detection methods. The results demonstrate that the system can effectively identify even the smallest leaks by measuring flow rates as low as nL/min and detecting pressure drops to enable precise leak rate quantification.
Fluigent’s systems offer integrated automation, ensuring both reliability and ease of integration into industrial quality control processes. This combination of precision, sensitivity, and automation positions Fluigent products as ideal solutions for the characterization of microfluidic systems, whether for development purposes or for the design of test benches.
Related products
References
[1] Xia Y, Chu X, Zhao C, et al. A Glass-Ultra-Thin PDMS Film-Glass Microfluidic Device for Digital PCR Application Based on Flexible Mold Peel-Off Process. Micromachines (Basel). 2022;13(10):1667. doi:10.3390/mi13101667
[2] Dekker S, Buesink W, Blom M, et al. Standardized and modular microfluidic platform for fast Lab on Chip system development. Sensors and Actuators B: Chemical. 2018;272:468-478. doi:10.1016/j.snb.2018.04.005
[3] van Heeren H, Lagrauw R, Silvero V. A Microfluidics Association white paper. Published online 2022.
[4] Daugbjerg TS, Ogheard F, Batista E, van Heeren H, Silverio V. MFMET Deliverable 1 – Guidelines and a Test Protocol for Flow Control Evaluating Leakage and Burst Pressure in Microfluidic Devices. Zenodo; 2023. doi:10.5281/zenodo.7901265