Flow Control Technologies: Comparison between peristaltic, syringe and pressure pumps for microfluidic applications
As the field of microfluidics continues to evolve, the mastery of various flow control technologies becomes increasingly crucial for the successful execution of microfluidic experiments.
In this Expertise Review, we aim to provide a comprehensive examination of the latest advancements and research pertaining to microfluidic flow control technologies. Our goal is to present an in-depth analysis of key findings and their implications for the future of microfluidics.
Introduction to Flow Control Technologies in Microfluidics
Why is it important to precisely control the flow?
In microfluidics, we aim to control the flow of fluids through channels with sub-millimeter dimensions in order to perform various kind of experiments, such as monodisperse droplet generation or organ-on-a-chip studies. In order to generate robust and reproducible data, precise control over the flow parameters is required: for example, the flow rates applied in the system will define the dimensions of the produced droplets, or generate a specific shear-stress on the cells, affecting their growth, spatial organization, and protein secretion. An error in the flow rates applied to the system can lead to polydisperse droplets, unstable systems, damaged cells, and more generally, to the failure of the experiment. Complete and reliable flow control is therefore essential in any microfluidic system.
What are the main microfluidic flow control technologies?
Various technologies, relying on different mechanisms, allow for fluid injection into microfluidic channels. However, they do not all provide the same level of control, as they rely on different physics:
- Applying pressure to fluids in a sealed container with a fluid outlet. The fluids will move because of the pressure difference, according to a simple relation, similar to Ohm’s law for electricity (V=RI): In the case of fluid flow, P=RQ. The fluidic resistance is a function of the geometry of the channel and the viscosity of the fluid. For more information, visit our microfluidic resistance page.
- Using volumetric control with syringe pumps or peristaltic pumps. Here the principle is to use a mechanical movement that modifies a volume to apply a flow rate. For syringe pumps, the syringe volume and the infusion rate can be modified to achieve different flow rates.
- Other techniques, such as electro-osmotic pumps or integrated micropumps, are used for more specific needs and are described below [1].
To achieve the best results in flow-based microfluidic experiments, it is important to consider the following elements:
- The flow rate or the pressure range you need.
- How quickly you need to set or change the flow rate.
- How stable you need the flow rate to be.
Based on these methods, different microfluidic flow control techniques and technologies are available to manage microfluidic flows.
Selecting the right microfluidic pump
The main flow control solutions can be divided into three categories: volume displacement (such as syringe or peristaltic pumps), pressure-based solutions (such as the Flow EZ™), and passive techniques.
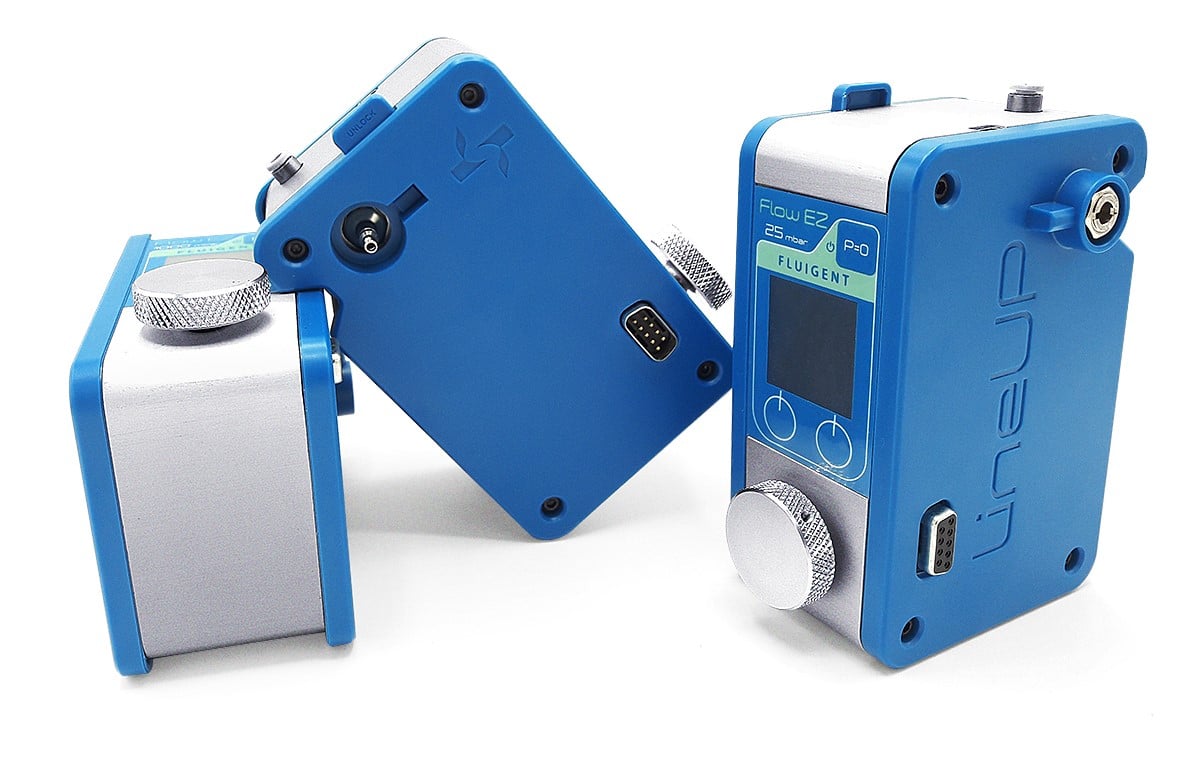
Strengths and weaknesses of each flow control technology
This pump selection guide shows the advantages and disadvantages of each method of fluid delivery in Microfluidics to help you choose the right one for your microfluidic application [2].
1. Fluid volume displacement in microfluidics
Fluid volume displacement, a common technique in microfluidic flow control, uses mechanical parts to directly displace a certain volume of fluid. The two main types of pumps using this approach, the peristaltic and the syringe pump, allow the user to control flow by indicating a flow rate as an input.
1.1. Syringe pump
Syringe pumps are good for the injection of small volumes, but they are less precise than pressure pumps, particularly at very low flow rates. A wide range of quality and prices are available on the market.
In microfluidic flow control, syringe pumps are based on a mechanical system actuated by a stepper motor, which pushes a syringe at a precise rate, allowing for a wide range of flow rates. However, the mechanical actuation can generate flow pulsations and have long response and settling times, particularly in the presence of air bubbles, viscous liquids, and compliant tubing.
Additionally, the actual flow rate within the system is not monitored, which can lead to bias if flow rate orders are not reached due to leakage, clogs, or incorrect set-up. The pressure is also not controlled, and if the microsystem becomes clogged, the pressure can rise to damaging levels. The text advises users to regularly check for blockages, particularly when using microparticles, and to be aware of the potential limitations of the technology when automating experiments.
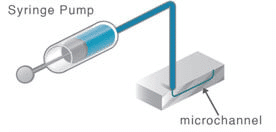
Syringe pumps in microfluidics have strengths and weaknesses. Some of them are listed below:
Strengths of microfluidic syringe pumps
- High limit of pressure (depending on syringe material)
- No variation of the syringe rate
Weaknesses of microfluidic syringe pumps
- Pulsatile flow
- Control of the flow in dead-end channels is impossible
- Difficult to determine the exact pressure inside of the microfluidic component
1.3. Peristaltic pump
Peristaltic pumping is based on the compression and the relaxation of flexible tubing. Rotating rollers pass along the tubing fitted inside the pump and compress it, creating a vacuum in the tubing and pulling the fluid along. This method of fluid actuation may be used in microfluidic laboratories and is rather inexpensive.
In microfluidic flow control, peristaltic pumping is a good option for large volumes and high flow rates, as well as for fluid recirculation. However, the compression of the tubing induces pulses in the flow, which is not suitable for most microfluidic applications where flow precision is important. Moreover, the flexible tubing should be changed regularly to prevent tube damage.
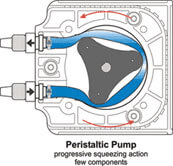
Strengths of peristaltic pumps for microfluidic flow control
- Easy to setup
- Large quantities of sample can be injected
Weaknesses of peristaltic pumps for microfluidic flow control
- Low reproducibility of the experiment
- The flow rate is not constant due to stretching of the tubing
2. Pressure-Driven Flow Controller Solution
Fluid actuation by pressure-driven flow controllers consists of pressurizing reservoirs containing the sample so it is then rapidly injected into a microfluidic device. The size of this reservoir is very flexible, ranging from 1.5/2ml Eppendorf tubes to 15/50ml Falcon vials and even larger bottles of several hundred milliliters.
To achieve microfluidic flow control, the controlled gas pressure pushes the fluid, which then flows through the reservoir outlet. Due to the excellent regulation provided by gas pressure controllers, these systems can achieve highly stable flow rates from sub-nanoliter/min to tens of milliliter/min (for example, Fluigent MFCS-EZ™ and LineUp™ have resolutions as low as 7×10-3 mbar). Moreover, users can control the flow rates directly if a flow sensor is coupled with the pressure controller. The pressure will be adjusted via powerful algorithms such as Fluigent FRCM and DFC. In addition, fluid recirculation is possible with valves (see Fluigent valve solutions) coupled to the pressure controller.
The main advantage of pressure pumps is that the user can pressurize multiple reservoirs with only one pressure channel. This can significantly reduce the cost of your setup if you want to inject different solutions sequentially.
For instance, all our MFCS™ series offer settling times down to 100ms and a resolution of 0.03% full scale (pressure sensor resolution), as well as a stability of 0.1% CV on measured values.
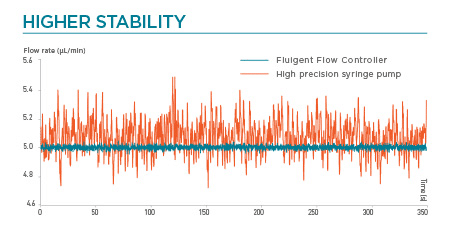
Pressure pumps in microfluidics have strengths and weaknesses. Some of them are listed below:
Strengths of pressure pumps in microfluidics
- Pulse-free flow control : there is no oscillation flow
- Both pressure and flow rate control in one device
- Very good stability : 0.005%
- Controls of the flow in dead-end channels is possible
- Ability to determine the exact pressure inside of the microfluidic component
Weaknesses of pressure pumps in microfluidics
- Limited to 8 bars
- Flow switches with multiple entry points can potentially cause back flow
3. Passive methods for microfluidic flow control and microfluidic flow measurement
3.1. Electro-osmotic pump
The principle is to create an electro-osmotic flow in a porous medium made of glass. An electric potential is applied between the porous media (up to several kV) and a flow rate is generated depending on the liquid’s ionic strength. The main advantage is that there are no moving parts, and the pump can be controlled directly with an electric signal. The main drawback is that it works only with water or alcohol with ionic species. The relation between the flow rate and the applied voltage depends on the ionic force; in practice, it can only be used for liquids with constant chemical properties, and calibration is needed.
3.2. Using hydrostatic pressure
This is the simplest way to move fluids: the basic idea is to put the inlet reservoir higher than the outlet reservoir in order to let gravity force move the fluid from the inlet to the outlet, just like a water tower.
4.Integrated micropump
In microfluidic flow control, several kinds of integrated micropumps exist, mostly based on a peristaltic principle with flexible membranes made of PDMS. The flow rate range is typically low, but can reach 10 to 100uL/min. The main advantage is the ability to control fluids down to the pL (10-12 L) range. It is particularly useful for applications where a very small quantity of fluid is to be tested. Integration into the microsystem involves complex steps of micromachining and requires a dedicated design specific to the desired application.
Overall, to make the best choice concerning the microfluidic flow control technology that best fits your experiment, it is important to consider the following elements:
- The flow rate or the pressure range you need.
- How quickly you need to set or change the flow rate.
- How stable you need the flow rate to be.
Microfluidic Flow Control: Advantages and disadvantages of each type of microfluidic pumps
Peristaltic Pump | Syringe Pump | Pressure driven Pump | |
---|---|---|---|
Flow stability | Bad | Medium | Excellent |
Response time | High | Low | Excellent |
Precision | Bad | Medium | Excellent |
Volume limitation (for the liquid to be injected) | No (you can use open reservoirs) | Yes (depends on the syringe volume) | No (you can use big bottles) |
Fluid recirculation | Possible | Not Possible | Not Possible (But you can use the L-switch (recirculation valve) |
Injection of small volume sample | Bad | Good (use very small volume) | Medium (difficult for less than 10µL) |
Gas injection | No | No | Yes |
Sample agitation | Possible (as the sample is in separated reservoir) | Not Possible | Possible (as the sample is in separated reservoir) |
Sample T°C control | Possible (you can put the reservoir in thermal bath) | Not Possible | Possible (you can put the reservoir in thermal bath) |
Possibility to create (program) complex flow profile | No | No | Yes (LineUp Series) |
Flow pressure control | No | No | Yes |
Flow rate control | Yes (need calibration) | Yes | No (possible if you add a flow sensor) |
High flow rates | Yes | Not suitable as it is difficult to refill the syringe | Yes |
Forward and Back flow | Yes | Yes (depends on the model) | Yes (but needs to pressurize the outlet too) |
Hydrostatic pressure influence | No | No | Yes (there is a lot of tips and tricks to avoid it) |
Tips for improving your pressure pump
Multiple solutions are offered in the microfluidic universe to help you to monitor your setup and your pressure pump. Fluigent has developed a large range of products to allow you to construct your system in a modular fashion.
If you want to use your pressure pump to:
- Control Flow Rate: you can add a microfluidic flow sensor that will measure the flow rate. Moreover, some software packages are available to allow you to adjust the pressure until you reach the desired flow rate.
- Stop the flow into the microfluidic chip: one can add a switch to the setup that can rapidly stop the flow in the microfluidic device without any backflow or residual flow.
- Improved flow switching: Switches can be added to the setup to allow for changing between two or more fluids. Those microfluidic valves are available with a large range of possibilities in terms of port number and allow one to employs multiple techniques such as sorting and recirculation.
- Monitor and control pressure: it’s possible to add a pressure generator to the microfluidic pressure pump to control the pressure inlet
- To obtain monodispersed droplets: you can add a surfactant to your samples in order to have long term stable microdroplets and to increase their frequency.
Tips for improving your microfluidic setup
Some common issues are encountered when running a setup. Microfluidic experts have developed tools to solve those problems and help you to have the most efficient setup possible.
If you want to :
- Avoid bubbles in your microfluidic setup: gas bubbles in a liquid sample are a common problem encountered in numerous microfluidic experiment, and their removal in the sample of interest is quite often a major challenge for microfluidics. Indeed, gas bubbles circulating through a microfluidic system can damage equipment or the biological sample of interest and cause experimental errors. Multiple accessories are available on the microfluidic market such as our Bubble Trap Kit or Degasser.
- Hand-free operation: tools are available to start/stop the flow or switch configuration of microfluidic devices with your foot.
- Automate your setup: The automation of your setup is possible thanks to some software tools that are able to monitor every compatible component of the setup.
- Unique software: has been designed to facilitate your manipulations and allows you to monitor your microfluidic devices in real time.
- Integrate microfluidic component to your setup: use OEM (Original Equipment manufacture) products to integrate them in your setup or devices.
Choosing the right materials for microfluidic chips
Since its introduction, microfluidics has continued to advance along with technology and to expand its fields of application. Along with other areas, biological and medical applications are a major focus of current research. In terms of materials and functions, while glass and silicon have important uses, polymeric materials have become the material of choice in this field. They each have their own advantages and disadvantages. Though PDMS is still the most commonly used microfluidic material substrate for microfabrication of chip, new materials and composites with interesting features are being developed to make them a better fit for mass production, with lower prices and greater adaptability.
Flow Rate Measurement in microfluidics
In microfluidic flow control, live flow monitoring can be achieved using flow sensors. The solution sold by Fluigent is called the Flow Unit, and can be used with the FRP or directly with the LineUP series for direct flow rate control.
There are an immense variety of microfluidic flow sensors based on different principles of physics. Not all of them are suitable for flows in microchannels. Choosing the right microfluidic flow meter for the desired flow regime and fluid is critical for accurate measurements. The following sections will describe some of the main technologies used for flow measurement. These solutions can be divided into thermal and non-thermal approaches.
1. Thermal sensors for flow measurement in microfluidics
One of the most common microfluidic flow control technology is based on the calorimetric method.
A micro heater supplies a minimal amount of heat to the medium monitored (around 1°C). Two temperature sensors located on either side of the heater detect any temperature variation. The flow rate is then calculated based on the spread of heat, which is directly related to the flow rate.
This method of monitoring the flow is one of the simplest and least intrusive. It is quite easy to integrate in MEMS devices, since very small heaters and sensors already exist. Nevertheless, this microfluidic flow control technique requires knowledge of the fluid’s density and specific heat capacity. These values also need to be constant for the sensor to function properly. In biological experiments, the presence of cells or particles in the fluid might affect the fluid properties and affect the measurement.
Several other thermal flow meters exist and function in a similar way [4]. The hot wire flow meter uses a resistor as heater and sensing element. Because the resistance is dependent on the temperature, a relationship can be established between applied voltage, temperature and resultant resistance. Other sensors use so-called “time-of-flight sensing”. This microfluidic flow control technique, illustrated in the figure, uses only one sensor that is located downstream of the heater. By observing the heat distribution over time, it is able to deduce the fluid velocity and thus the flow rate.
2. Mechanical flow sensors for flow measurement in microfluidics
One of the most important categories of non-thermal flow measurement techniques is mechanical flow sensors. Since flow is usually laminar in microfluidics, laws to calculate the drag force on the channel walls and the pressure drop in the direction of flow are known. Both drag and pressure drop are directly related to the flow velocity. By using piezoresistive transducers or integrated pressure sensors, it is possible to deduce the flow velocity and thus the flow rate in the sensor [5].
3. Coriolis mass flow meters in microfluidics
The use of mass flow meters in microfluidic flow control is growing as the technology continues to improve for use with microscale flows. In a mass flow meter operating on the “Coriolis principle”, the fluid flows on a vibrating channel. The Coriolis force acting on the moving fluid will affect the frequency, phase shift or amplitude of the initial vibration proportionally to the mass flow rate.
The main advantage of Coriolis mass flow meter is the independence between the measured flow rate and the properties of the liquid. These sensors can monitor gas or oil flows without any specific calibration. However, the technology remains expensive and the small inner diameter of the fluidic path might not be suitable for biological experiments.
4. Other technologies for flow control or flow measurement in microfluidics
Apart from mechanical technologies, there are also many other non-thermal solutions for flow measurement. Some of them involve optics, acoustics or electrochemical phenomena.
Conclusion
We have seen that there are a variety of flow rate control solutions when it comes to flow control and flow measurement. Our goal in this review was to show the strengths and weaknesses of the main technologies used in microfluidics. For flow control, the main solutions used in microfluidics are mechanical or pressure-based. Mechanical solutions allow for direct microfluidic flow control, but do not control the pressure that is applied to the fluid and lack stability. Pressure-based solutions ensure higher stability and faster response times, and can even monitor and control the flow rate directly with the help of an additional flow sensor. Many different microfluidic flow sensor technologies have been studied and developed. The two main categories are thermal and mechanical sensors. Depending on the desired flow rates and regimes, users must evaluate the right choice of sensor for each experiment.
Related Products
Expertises & Resources
References
- Beebe, D. J., Mensing, G. A., & Walker, G. M. (2002). Physics and applications of microfluidics in biology. Annual review of biomedical engineering, 4(1), 261-286.s. Lab on a Chip, 2008
- Li et al, Lab Chip 2014, 14, 744
- X. Li et al, Biomicrofluidics, 2012, (6)
- Jonathan Kuo et al, Micromachines 2012, 3(3), 550-573
- Nguyen, Flow Measurement and Instrumentation, 1997, 8(1), 7-16