Mikrofluidik für hohe Flusskontrolle
Mikrofluidik ist die Wissenschaft und Technologie, die sich mit der Untersuchung von Flüssigkeiten in Mikrokanälen befasst und kleine Flüssigkeitsmengen (10-6 bis 10-12 L) mithilfe mikrominiaturisierter Geräte verarbeitet oder manipuliert, die Kammern und Kanäle für den Fluss oder den Flüssigkeitseinschluss enthalten.
Wie funktioniert die Mikrofluidik?
Die Mikrofluidik befasst sich mit der sehr präzisen Steuerung von Flüssigkeiten auf kleinstem Raum und Volumen. Mikrofluidik-Chips sind Geräte, die in mikrofluidischen Studien verwendet werden und in denen Mikrokanäle geformt oder gemustert wurden. Die Mikrokanäle sind so miteinander verbunden, dass Flüssigkeiten durch die verschiedenen Kanäle fließen und sich von einem Ort zum anderen bewegen können. Dieses Netzwerk ist über Einlass- und Auslassöffnungen mit der äußeren Umgebung verbunden. Die Flüssigkeiten oder Gase werden über passive Wege oder externe aktive Systeme (Druckregler, Spritzenpumpen oder Peristaltikpumpen) in den Mikrofluidik-Chip injiziert, gesteuert oder aus ihm entfernt.
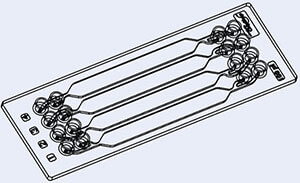
Die Kanäle können unterschiedliche Innendurchmesser haben, die in der Regel zwischen 5 und 500 μm liegen und ihr Netzwerk muss speziell für die jeweilige Anwendung und die durchzuführende Analyse ausgelegt sein. Daher ermöglichen mikrofluidische Chips die Integration mehrerer Funktionen, für die normalerweise ein ganzes Labor benötigt wird, in einem einzigen Gerät in Mikrogröße.
Was ändert sich für Flüssigkeiten im mikrometrischen Maßstab?
Im mikrometrischen Maßstab ändert sich das Verhalten von Flüssigkeiten und bietet mehrere Vorteile: eine schnelle Wärmeübertragung, ein größeres Verhältnis von Oberfläche zu Volumen, ein laminarer Fluss und eine mögliche Diffusionsmischung. Darüber hinaus verringert die Mikrofluidik den Proben- und Reagenzienverbrauch erheblich, verkürzt die Versuchsdauer und reduziert die Gesamtkosten der Anwendungen.
Dank der Entwicklung der Mikroelektronik und der Miniaturisierung von Transistoren wurde dieses Konzept mit der Einführung des „Lab-on-Chip“-Prinzips (LoC) und des „Micro Total Analysis System“ (μTAS) auf den biomedizinischen und chemischen Bereich übertragen. Zu den ersten Beispielen für mikrofluidische Chips gehörten S. Terry et al., die 1979 einen Chip auf einem Silizium-Wafer entwickelten, der die Funktionen eines Gaschromatographen miniaturisierte. Seit dieser Pionierarbeit erlebte die Mikrofluidik ein explosionsartiges Wachstum und wurde zu einem unverzichtbaren Werkzeug sowohl für akademische Forscher als auch für Industrieunternehmen.
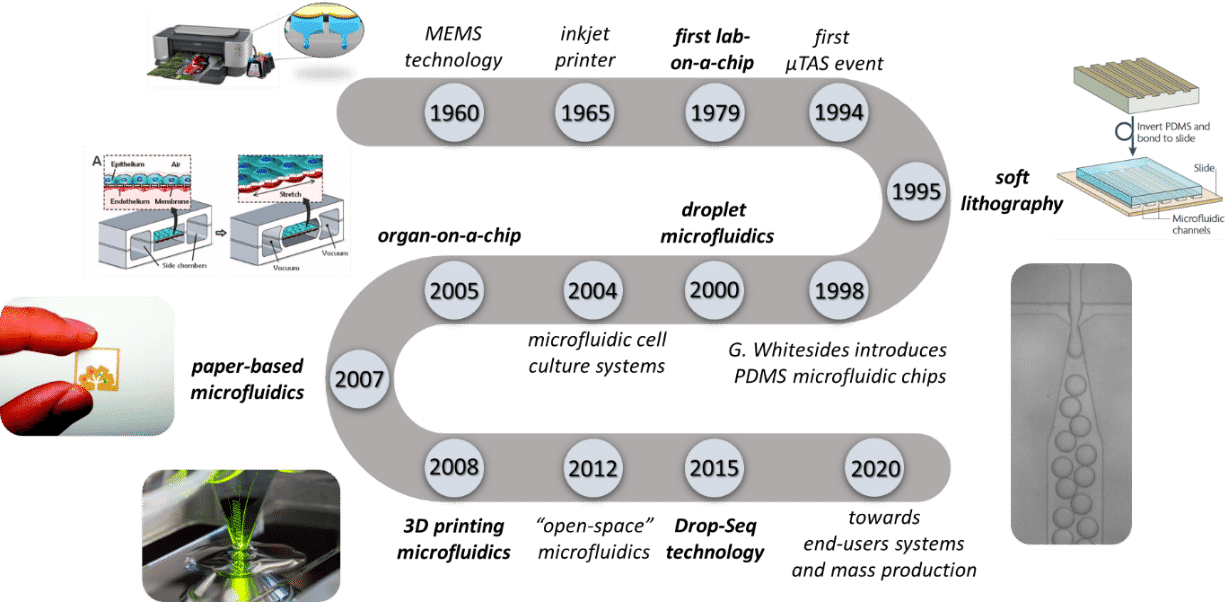
Die Entwicklung der Mikrofluidik
Was sind die Vorteile der Mikrofluidik?
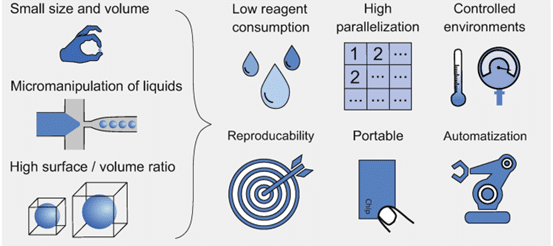
Vorteile der Mikrofluidik [1]
Das Schlüsselkonzept der Mikrofluidik ist die Integration von Vorgängen, für die normalerweise ein ganzes Labor benötigt wird, in ein einfaches, mikrokleines System. Derzeit wird das herkömmliche Scale-up in mikrofluidischen Systemen durch Multiplexing ersetzt, da die kompakte Größe des Geräts die Zeit von der Formulierung bis zur Produktion drastisch verkürzt. Dies führt dazu, dass mikrofluidische Technologien nicht nur für analytische Zwecke, sondern auch in der Prozessindustrie, insbesondere in der Feinchemie, der Lebensmittel-, Umwelt- und Pharmaindustrie für die Herstellung in großem Maßstab eingesetzt werden. In den letzten Jahren wurden mikrofluidische Geräte auch in großem Umfang als Analyseinstrumente für biochemische und molekularbiologische Anwendungen eingesetzt.
Mikrofluidische Systeme bieten außerdem eine hervorragende Datenqualität und eine verbesserte Parameterkontrolle, die eine Prozessautomatisierung unter Beibehaltung der Leistung ermöglicht. Sie sind in der Lage, Proben mit geringem Aufwand sowohl zu verarbeiten als auch zu analysieren. Die Verbindung zwischen dem mikrofluidischen Chip und dem Fluid-Handling-System ist so konzipiert, dass die eingebaute Automatisierung es dem Benutzer ermöglicht, mehrstufige Reaktionen durchzuführen, die ein geringes Maß an Fachwissen und eine Vielzahl von Funktionen erfordern.
So bietet die Mikrofluidik beispielsweise eine höhere Empfindlichkeit bei der Wasseranalyse im Vergleich zu herkömmlichen Methoden und die Möglichkeit, geringere Schadstoffkonzentrationen zu erkennen. Die Analysezeit wird drastisch verkürzt, was eine Überwachung in Echtzeit und eine höhere Effizienz ermöglicht und gleichzeitig eine Wasserverschwendung durch sehr kleine Proben verhindert.
Darüber hinaus wird erwartet, dass mikrofluidische Technologien in Zukunft eine wichtige Rolle bei der Herstellung und Verabreichung von therapeutischen Produkten und Diagnostika im Bereich der Nanomedizin spielen werden, da sie die Nachfrage nach qualitativ hochwertigen und sorgfältig regulierten medizinischen Produkten erfüllen.
Wie man diese Vorteile der Mikrofluidik nutzen kann.
In der Mikrofluidik wird die Beherrschung verschiedener Technologien zur Flusskontrolle im Mikrometermaßstab immer wichtiger für die erfolgreiche Durchführung von Mikrofluidikexperimenten. Um robuste und reproduzierbare Daten zu erhalten, ist eine präzise Kontrolle der Flussparameter erforderlich. So bestimmen die im System angewendeten Flussraten beispielsweise die Größe der erzeugten Tröpfchen oder erzeugen eine spezifische Scherbeanspruchung der Zellen, die sich auf ihr Wachstum, ihre räumliche Organisation und ihre Proteinsekretion auswirkt. Ein Fehler bei den Flussraten des Systems kann zu polydispersen Tröpfchen, instabilen Systemen, beschädigten Zellen und ganz allgemein zum Scheitern des Experiments führen. Eine vollständige und zuverlässige Flusskontrolle ist daher in jedem mikrofluidischen System unerlässlich.
Welche Systeme werden in der Mikrofluidik am häufigsten für die Flusskontrolle eingesetzt?
Spritzenpumpen
Spritzenpumpen eignen sich gut für die Injektion kleiner Volumina, sind aber weniger präzise als Druckpumpen, insbesondere bei sehr niedrigen Flussraten. Auf dem Markt gibt es eine große Auswahl an Qualität und Preisen.
Bei der mikrofluidischen Flusskontrolle basieren Spritzenpumpen auf einem mechanischen System, das von einem Schrittmotor angetrieben wird, der eine Spritze mit einer präzisen Geschwindigkeit vorschiebt und eine große Bandbreite an Flussraten ermöglicht. Die mechanische Betätigung kann jedoch Flusspulsationen erzeugen und lange Reaktions- und Einschwingzeiten haben, insbesondere bei Vorhandensein von Luftblasen, viskosen Flüssigkeiten und nachgiebigen Schläuchen. Darüber hinaus wird die tatsächliche Flussrate im System nicht überwacht, was zu einer Verzerrung des Ergebnisses führen kann, wenn die geforderte Flussrate aufgrund von Leckagen, Verstopfungen oder einer falschen Einstellung nicht erreicht wird. Auch der Druck wird nicht kontrolliert, und wenn das Mikrosystem verstopft ist, kann der Druck auf ein schädliches Niveau ansteigen. Es wird den Nutzern geraten, regelmäßig auf Verstopfungen zu achten, insbesondere bei der Verwendung von Mikropartikeln, und sich der möglichen Grenzen der Technologie bei der Automatisierung von Experimenten bewusst zu sein.
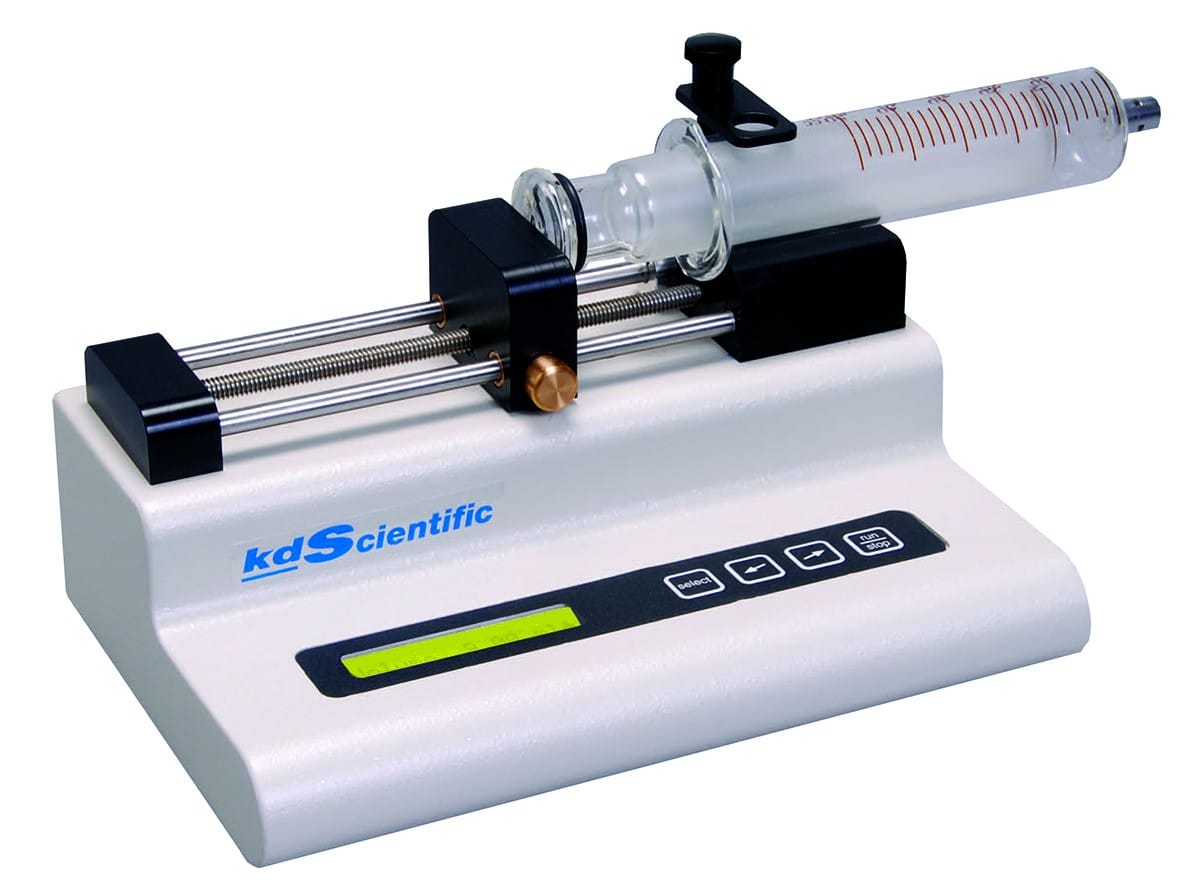
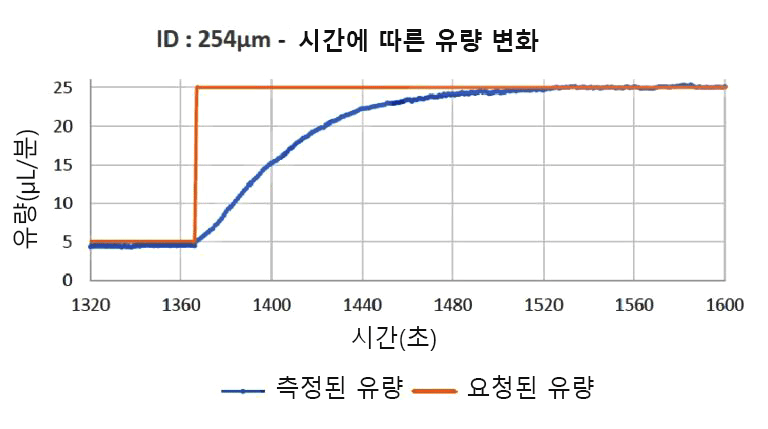
Diagramm der Ansprechzeit einer Spritzenpumpe
Peristaltische Pumpe

Peristaltische Pumpe
Die peristaltische Pumpe basiert auf der Kompression und Entspannung eines flexiblen Schlauchs. Rotierende Rollen laufen an dem in der Pumpe angebrachten Schlauch entlang und komprimieren ihn, wodurch ein Vakuum im Schlauch entsteht und die Flüssigkeit mitgerissen wird. Diese Methode der Flüssigkeitsbetätigung kann in mikrofluidischen Labors eingesetzt werden und ist relativ kostengünstig.
Bei der mikrofluidischen Flusskontrolle ist die peristaltische Pumpe eine gute Option für große Volumina und hohe Flussraten sowie für die Rückführung von Flüssigkeiten. Die Kompression der Schläuche führt jedoch zu Impulsen im Fluss, was für die meisten mikrofluidischen Anwendungen, bei denen die Flussgenauigkeit wichtig ist, nicht geeignet ist. Außerdem sollten die flexiblen Schläuche regelmäßig ausgetauscht werden, um eine Beschädigung der Schläuche zu vermeiden.
Druckregler-Lösung
Bei der Flüssigkeitsbetätigung mit druckgesteuerten Flussreglern werden Behälter, die die Probe enthalten, unter Druck gesetzt, so dass sie schnell in ein mikrofluidisches Gerät injiziert wird. Die Größe dieses Behälters ist sehr flexibel und reicht von 1,5/2 ml Eppendorf-Röhrchen über 15/50 ml Falcon-Fläschchen bis hin zu größeren Flaschen von mehreren hundert Millilitern.
Um eine mikrofluidische Flusskontrolle zu erreichen, drückt der kontrollierte Gasdruck die Flüssigkeit, die dann durch den Auslass des Reservoirs fließt. Aufgrund der ausgezeichneten Regulierung durch Gasdruckregler können diese Systeme hochstabile Flussraten von bis zu einigen zehn Milliliter/min erreichen.
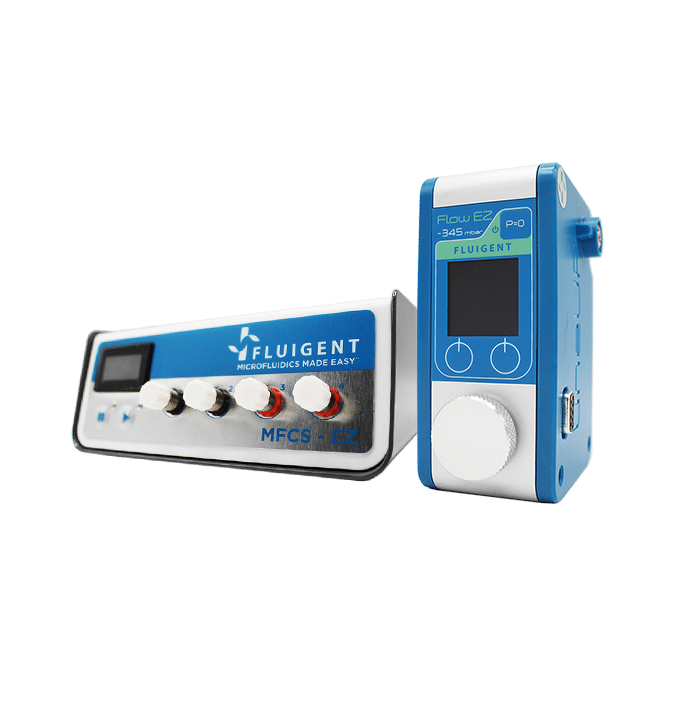
Fluigent’s MFCS und FLOW EZ Druckregler
Bei Fluigent präsentieren wir die druckgesteuerten MFCS-EZ™- und LineUp™-Regler, die eine Auflösung von nur 7×10-3 bar haben. So bieten alle unsere Serien Einschwingzeiten von bis zu 100 ms und eine Auflösung von 0,03 % des Skalenendwerts (Auflösung des Drucksensors) sowie eine Stabilität von 0,1 % CV auf die Messwerte.
Wenn ein Flusssensor mit dem Druckregler gekoppelt ist, kann der Anwender die Flussmenge direkt steuern. Der Druck wird über leistungsstarke Algorithmen wie Fluigent’s Oxygen eingestellt. Zusätzlich kann eine Flüssigkeitsrückführung durch die Verbindung unserer Ventile mit dem Druckregler erfolgen.
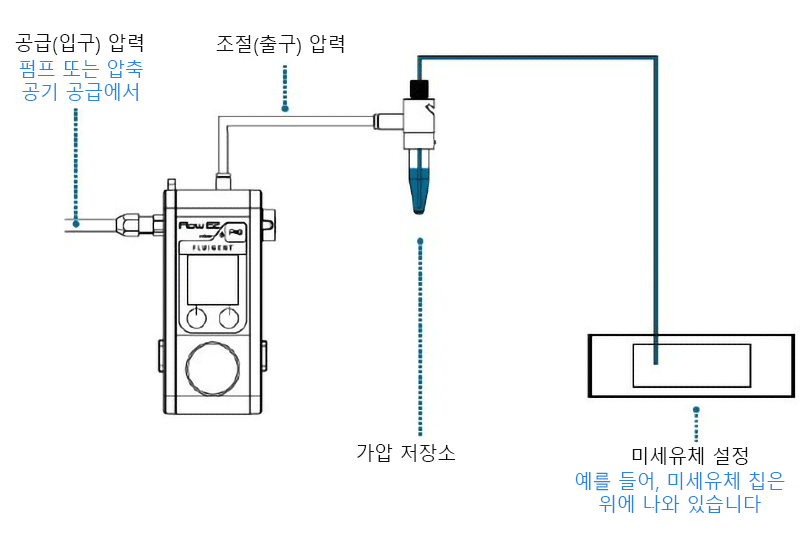
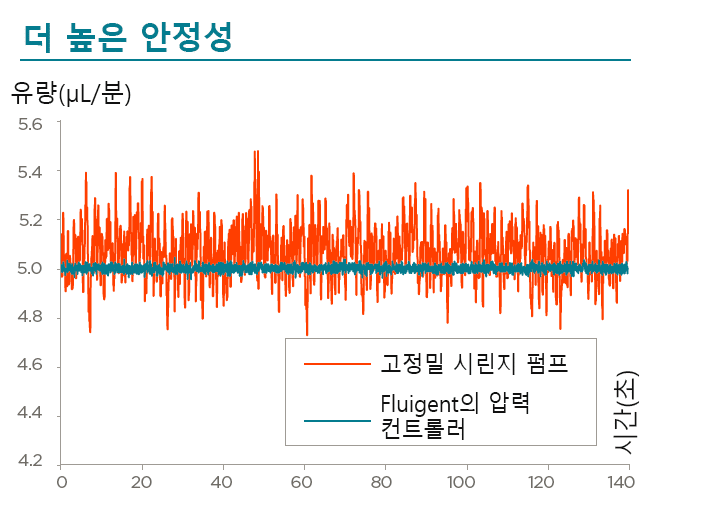
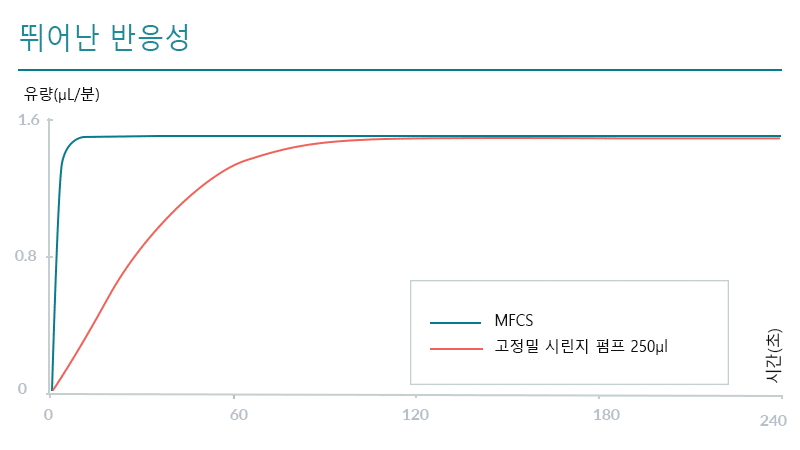
Ein weiterer Vorteil von Druckpumpen ist, dass der Benutzer mehrere Behälter mit nur einem Kanal unter Druck setzen kann. Dies kann die Kosten Ihrer Anlage erheblich reduzieren, wenn Sie verschiedene Lösungen nacheinander injizieren möchten. Aufgrund dieser Vorteile werden unsere druckbasierten Flussregler in Anwendungen eingesetzt, bei denen ein hohes Maß an Präzision und Kontrolle über die Parameter (Größe, Mischung, Flussraten usw.) erforderlich ist. Sie bieten hervorragende Ergebnisse bei Experimenten im Zusammenhang mit der Tröpfchenerzeugung, ddPCR, Zellkultur und Zellperfusion, Organ-on-a-Chip-Studien, Synthese von Nanopartikeln, Mikrokapseln und Mikroperlen.
Referenzen
1- Bahnemann, J.; Grünberge, A. Microfluidics in Biotechnology: Overview and Status Quo. Advances in Biochemical Engineering/Biotechnology book series, 2022, ABE,volume 179.