DFC, “Self-Learning” Microfluidic Flow Control Algorithm
Many microfluidic applications require liquid flow control through the monitoring and adjusting of the flow rate while an experiment is running to control the sample volume dispensed and/or the sample flow rate. The latest enhancement to our microfluidic flow rate control algorithm is a “self-learning” Direct Flow Control algorithm that fixes issues in microfluidic flow control including calibration, multi-channel interaction and resistance changes during experiments.
This algorithm is integrated into every custom project and users will benefit from Fluigent’s expertise throughout the experiment.
- Unmatched performance: excellent accuracy, stability and responsiveness
- Versatile: easy switch between pressure and flow rate control
- No manual calibration needed: automated adjustment of the parameters for lasting efficiency

Microfluidic flow rate control algorithm : technology description
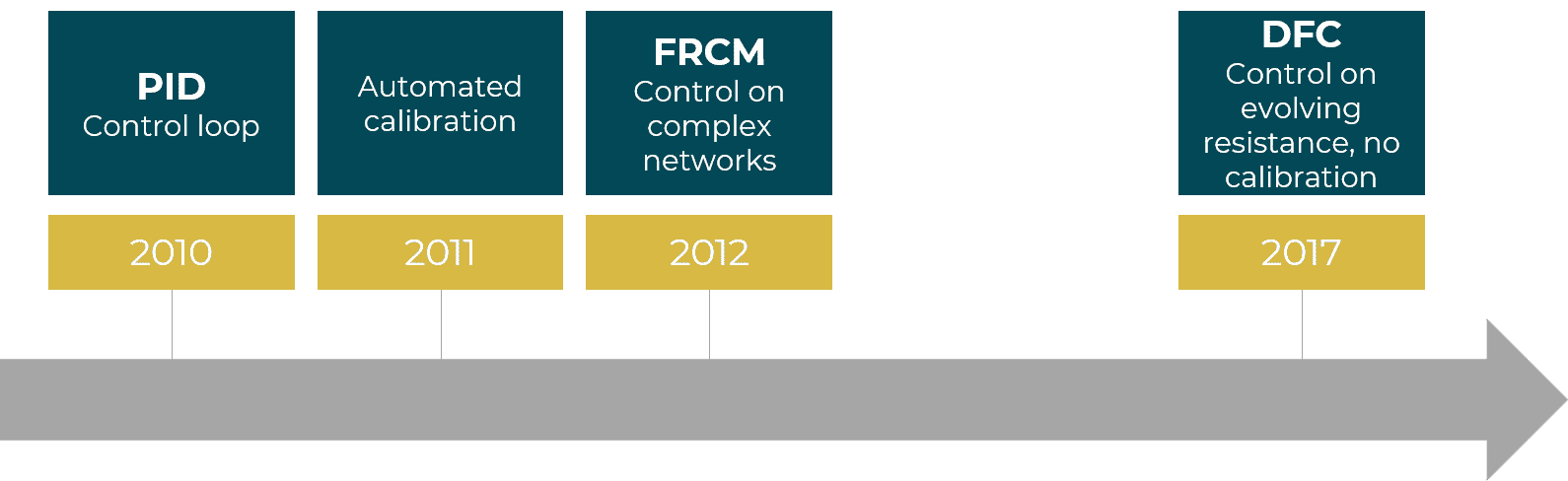
Fluigent’s first software (2010) had an integrated PID: a control loop mechanism that maintains a desired flow rate with minimal delay and overshoot by altering the pressure applied to a setup.
Fluigent’s first flow rate control scheme (2011) was improved to include an automated calibration procedure to calculate optimized PID parameters according to the hydrodynamic resistance of the system, i.e. the microfluidic channel dimension and the viscosity of the liquid. This meant that manual adjustments for flow rate response time and stability were no longer necessary to control the flow.
As microfluidic design increased in complexity, finding the calculation of the required pressure for the desired flow rate became difficult. The Flow Rate Control Module, or FRCM (2012), was the first microfluidic flow control algorithm that permitted pressure-based flow rate control on complex microfluidic channel networks like multi-channel setups, by predicting and automatically adjusting pressure(s) to reach the flow rate set point(s). The algorithm internally modeled a microfluidic system with any design and linked each flow rate to a combination of pressure orders. It was useful for droplet generators, double encapsulation systems or mass parallel systems.
Fluigent’s latest microfluidic flow rate control algorithm technology update (FASTAB2): Direct Flow Control
The DFC “self-learning” algorithm (2017) offers two major upgrades: (1) no calibration is needed and (2) it performs in a system where hydrodynamic resistance evolves along the experiment. This improvement to the auto tuned PID and the FRCM includes a continuous adjustment of the algorithm parameters based on the current response time and stability. Its improved reactivity allows it to counter the interactions between microfluidic channels in complex situations. Advantages of direct flow control algorithm include:
- Adapting to experiments with resistance variations like cell culture growth: the flow rate control algorithm, being a microfluidic self-learning algorithm, adjusts its model to the setup resistance in real-time
- Saving samples or reagents: reduced time to reach desired flow rate uses less liquid during a calibration step
- Saving time: no calibration required and a reduced settling time
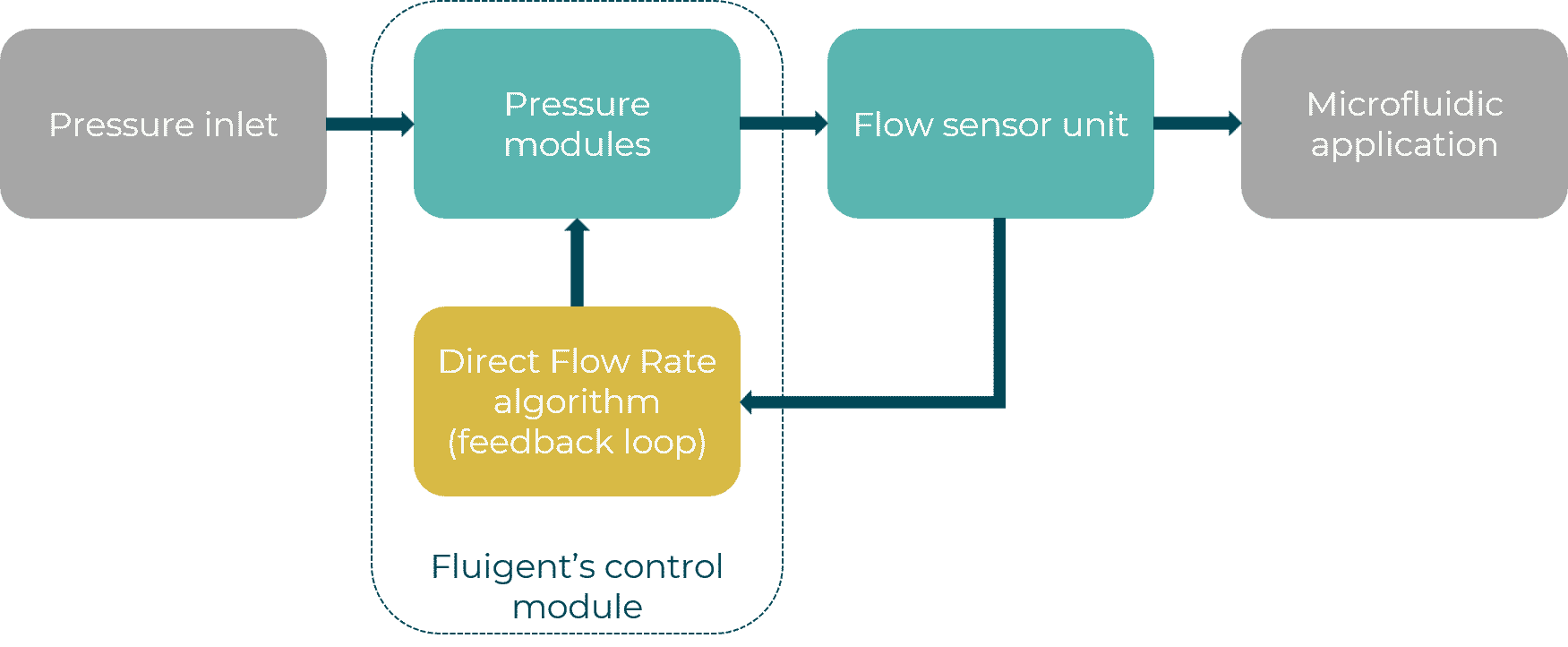
Microfluidic flow rate control algorithm performances
Optimizing an algorithm is time consuming. In microfluidic liquid handling, stability (no unbounded oscillation) and response time are prerequisites. Fluigent’s new direct flow control algorithm aims at achieving the best performances for each, providing a completely automated microfluidc system.
Maintaining the flow stability
When used with flow rate sensors, microfluidic pressure controllers maintain a highly stable flow rate. This achieves the same functionality as a syringe pump, with a more stable and reliable output for flow control. Increasing the stability of the flow rate improves the reproducibility of microfluidic experiments. This factor is essential in biological and chemical applications for reliable results. Flow rate stability is also essential to control cell shear stress: the tangential component of frictional forces generated at a surface by the flow of a viscous fluid, as it affects the physiology of the cells.
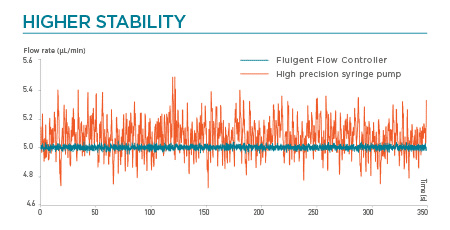
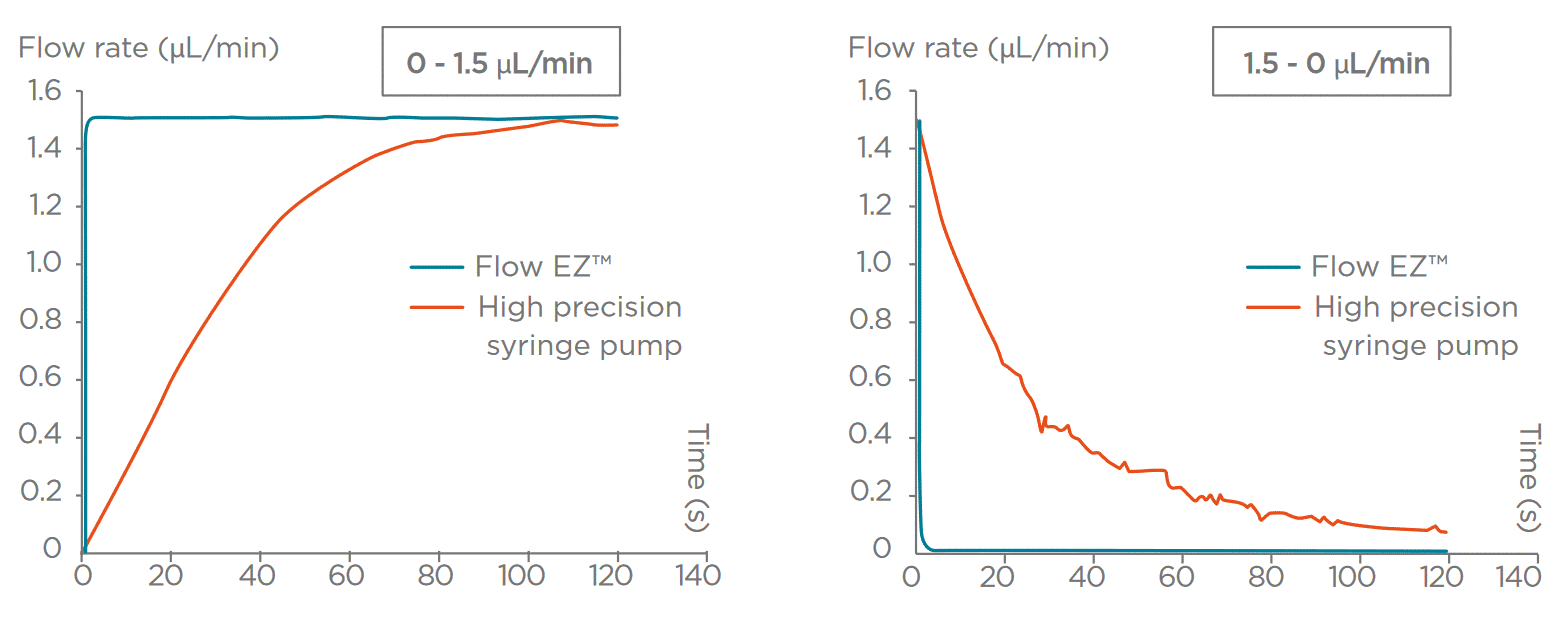
Providing excellent response time
Response time is the time required to reach an ordered value given an error margin. Pressure based Microfluidic Flow Controllers display major benefits in terms of responsiveness compared to other types of liquid handling solutions such as syringe or peristaltic pumps. The Flow Controllers reduce the elapsed time between the command and the desired flow rate and prevent the waste of samples. Thanks to our FASTAB2 patented flow control algorithm, the response time to reach the ordered value with 5% error is 2 seconds, which is more than twice as fast as the FRCM. This technology is over 10 times faster than the most advanced syringe pumps available on the market, as shown on the graphs below.
Pressure & liquid flow control
By combining both pressure and flow rate control/monitoring, Fluigent overcomes one major drawback of pressure pumps: the lack of having optimized direct control of flow rates. In just one click, a Fluigent pump can switch from pressure to flow rate control. This allows users to control either parameter with the best flow stability and response time available on the market, without the need for additional settings and complex microfluidic channel configurations. Unlike syringe pumps, flow sensors and Fluigent’s microfluidic flow control algorithm can predict pressure values and apply set flow rates.
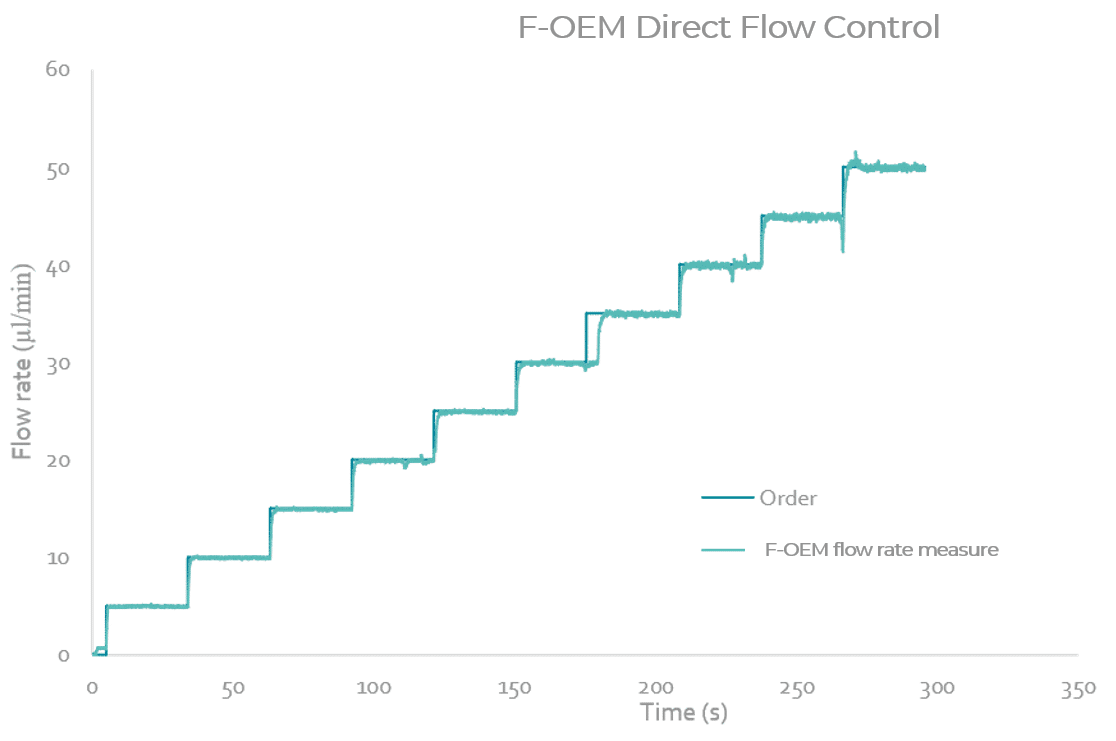
Related applications that could use our microfluidic flow rate control algorithm
Drug testing
Flow rate control is used for determining the time of exposure or for applying a chemical concentration gradient. Compared to conventional drug screening methods, a microfluidic-based system presents advantages in terms of sample consumption, responsiveness and cost. [1][2]
Droplet microfluidics
The flow rate determines droplet size, frequency, and monodispersity. With the level of control provided by a microfluidic flow control algorithm, applications like digital PCR or single-cell encapsulation within droplets have emerged. [3][4]
Cell culture experiments
High flow rates can lead to shear-stress, which impacts cell shape and growth, because dragging frictional force stimulates the release of vasoactive substances and modifies gene expression, cell metabolism and cell morphology. [5][6] For more information on shear stress and its impact on cell viability, see our mechanical stimulation expertise webpage. If you want to calculate the applied shear stress with your system, see our shear stress calculator.
References
[1] L. Yu, M. C. W. Chen, K. C. Cheung, “Droplet-based microfluidic system for multicellular tumor spheroid formation and anticancer drug testing”, Lab on a Chip, 2010
[2] Q. Sun, S. H. Tan, Q. Chen, R. Ran, Y. Hui, D. Chen, C. Zhao, “Microfluidic Formation of Coculture Tumor Spheroids with Stromal Cells As a Novel 3D Tumor Model for Drug Testing”, ACS Biometer. Sci. Eng., 2018
[3] R. Seemann, M. Brinkmann, T. Pfohl, S. Herminghaus, “Droplet based microfluidics”, Reports on Progress in Physics, 2012
[4] G. Pohl, leM. Shih, “Principle and applications of digital PCR”, Expert Rev. Mol. Diagn., 2004
[5] N. Ashammakhi, R. Nasiri, N. R. de Barros, P. Tebon, J. Thakor, M. Goudie, A. Shamloo, M. G. Martin, A. Khademhosseni, “Gut-on-a-chip: Current progress and future opportunities”, Biomaterials, 2020
[6] S. Halldorsson, E. Lucumi, R. Gómez-Sjöberg, R. M. T. Fleming, “Advantages and challenges of microfluidic cell culture in polydimethylsiloxane devices”, Biosens Bioelectron, 2015